制芯工艺
在日益增加的质量要求和薄壁复杂结构化的趋势下,导致更严苛的品质要求和复杂化砂芯结构。本文阐述了仿真如何优化芯盒设计,建立包括射砂、冷芯盒和热芯盒用的有机和无机粘结剂的吹气和固化过程在内的稳健工艺条件和解决方案。
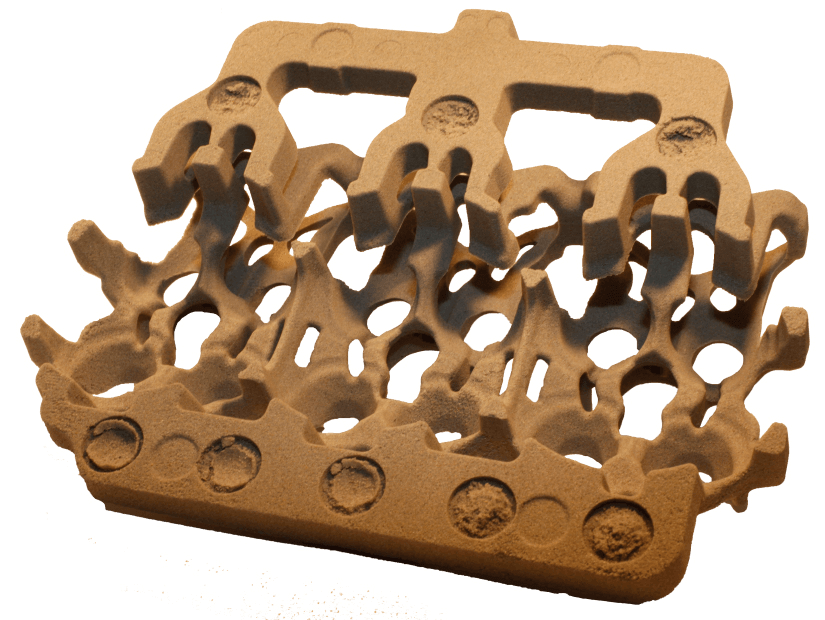
制芯工艺流程
射砂过程
在射砂过程中,一个装满砂的罩子的顶端被压缩空气加压,导致砂子流化,从而形成一种由空气、砂子和粘合剂的混合物。砂流通过射嘴进入芯盒内,并且最终通过排气塞逸出到大气中去。目标是尽可能获得均匀的、更紧实的芯盒密度。FLOW_3DCAST采用两相流理论模拟整个射砂过程,准确的分析高速气体的流动以及砂粒的流动,为其提供科学指导。借助FLOW-3D CAST软件,您可以优化参数(射砂压力、排气塞的大小及位置、射嘴的数量大小及位置)以获得稳健的设计参数和低磨损的模具,可以在不牺牲砂芯品质下尽可能少的使用射嘴,从而大大节省成本。通过仿真可以分析不同射嘴及排气塞的配置对砂芯密度分布的影响。通过预测速度和剪切应力,工程师可以得出磨损和寿命的结论。
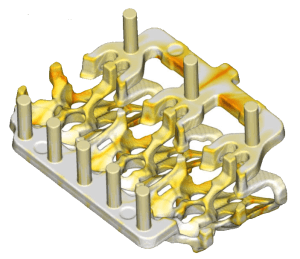
在有机粘结剂体系中,需要砂子与有机树脂均匀混合。树脂固化是由r种气体催化剂完成的,通常将胺气体从射嘴中注入,吹气需要足够长的时间,使胺气体能够到达每个部分,以确保砂芯全部硬化。同时为了节省有毒气体,吹气时间不应该过长。仿真可以预测砂芯内胺气体浓度分布.以评估砂芯强度。工程师借此确定一个合理吹气时
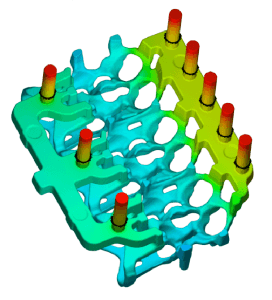
无机砂芯干燥过程
由于环保要求越来越高,越来越多的铸件使用无机的、水性的粘结剂替代有毒的、有机的粘结剂。其优点是可以接近零排放的工艺,同时减少铸造过程中砂芯发气,提高了铸件质量。对于砂芯硬化必须从砂芯中将水去除,通常通过注入加热空气方式实现。对于无机粘结剂系统,砂芯的残留水分是硬度测量指标。FLOW-3D CAST不仅可以考虑砂芯内空气流动,还可以考虑水和蒸汽的蒸发和冷凝过程,以及蒸汽与热空气的输送过程。
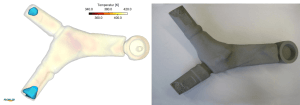
热芯盒和Croning的加热装置
在些砂芯制备, 比如热芯盒和Croning热固性树 脂砂,砂芯硬化是通过加热装置的芯盒中,加热到180~ 250C,使贴近芯盒表面的砂料受热,在温度作用下,其粘结剂在很短时间内即可缩聚而硬化粘合剂的热反应来完成的。加热过程是通过加热管和电加热元件进行的。为了获得高品质的芯盒,控制系统是一个得到均匀温度分布的核心。FLOW-3D CAST可以预测加热装置在工作条件下模具温度分布,为获得热量分配均匀提供了可靠依据。
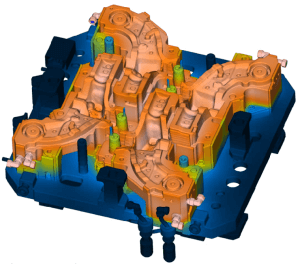
吹芯模型验证
水套芯的实验与仿真对比
在慕尼黑工业大学的铸造研究所正在进行一项射砂实验验证,分析了不同参数(比如,射砂时间、射砂压力、进口和排气塞的数量等工艺参数)对砂芯质量的影响。实际砂芯缺陷位置与仿真结果中的低密度区域相吻合(见下图)。
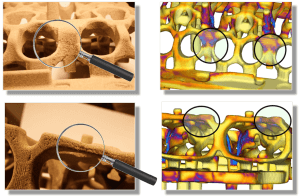
吹芯模型的应用
利用FLOW-3D CAST改善后桥壳体铸件质量
质保人员检测到后桥壳体铸件上存在缺陷(见下图),该缺陷可能是由砂芯表面缺陷造成。仿真结果也印证了这个假设观点,并根据仿真结果做出相应的砂芯表面质量的改善措施。最终通过排气塞优化配置(数量和位置),达到改善芯盒和铸件质量的要求。
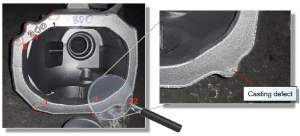
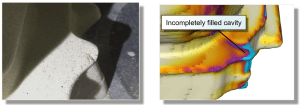
芯盒的寿命预测
芯盒主要是由铝和聚氨酯树脂混合制成。在射砂过程中砂粒将会对表面侵蚀,这是影响芯盒使用寿命。目标是分析侵蚀过程,了解表面处理对寿命的影响,并开发一个计算模型,预测由此造成的侵蚀问题。通用芯盒( 见下图)是用不同形状的嵌件构建的。
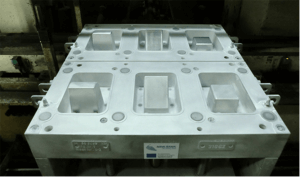
磨损数学模型是对表面压力和剪力的积分而推导出侵蚀深度。模拟预测结果与实验相吻合(见下图)
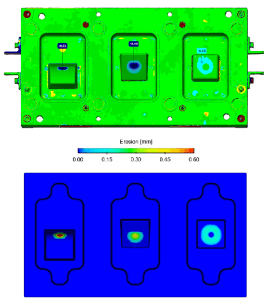
离心铸造
在离心铸造中,当熔融金属被注入高速旋转的模具时,熔融金属在离心力作用下,金属液沿着径向均匀地充满铸型,随后在离心运动作用下冷却凝固,生产出高致密度、低气孔、低夹渣等缺陷、良好力学性能的铸件。结合离心力作用下较高的压力及无需使用型芯工艺特点,有助于金属液中气体和夹杂物的排除,有助于金属结晶和细化晶粒,从而改善铸件的机械性能和物理性能。FLOW-3D CAST的非惯性参照系模型可以实现离心旋转过程,并具有灵活修改参数的能力,从而产生高精度的仿真结果。FLOW-3D CAST可以模拟卧式离心铸造和立式离心铸造。预测铸件欠铸、气孔、含气量、缩孔缩松、冷隔、氧化夹渣、偏析、变形、热裂等缺陷,从而为优化设计、改善生产工艺参数、降低研发和生产成本、提高铸件产品质量提供可靠的依据。
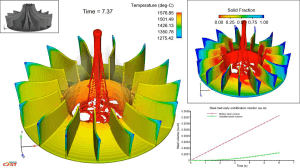
消失模铸造
消失模铸造因其近无余量、精确成型而越来越受欢迎,可用于生产高度复杂的、薄壁和细小特征的铸件。由于几乎不需要在型砂中使用粘合剂,型砂可以重复使用,从而大大节省成本。为了成功制造出完好铸件,工艺参数必须严苛控制。
FLOW-3D CAST提供消失模铸造的完整功能,精准预测褶皱或泡沫分解气化造成的缺陷。
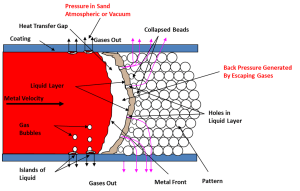
充型过程
许多铸件缺陷是由紊流造成并最终滞留在金属内部的气体和氧化物。消失模铸造工艺通过在型腔内放置硬质泡沫来减少这种缺陷,然后在熔体前沿的热辐射和热传递作用下燃烧气化。填充速度由热解速率控制,有助于金属前沿平稳流动。FLOW-3D CAST消失模铸造模块提供完整物理模型,为产品和工艺设计提供准确及有效的帮助,比如浇注温度及压力,浇口尺寸及位置,和泡沫物性。
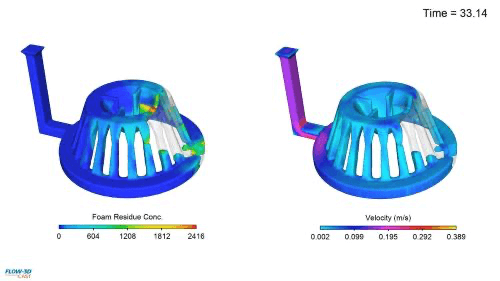
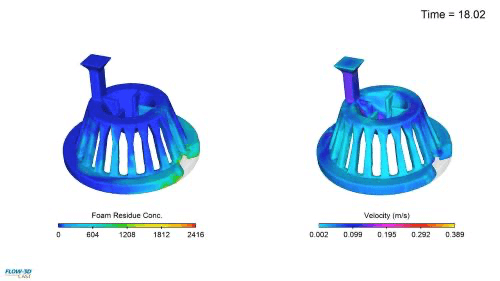
凝固过程
FLOW-3D CAST凝固有助于预测和控制铸造缺陷,如偏析、缩松、缩孔、和受其影响的机械性能。FLOW-3D CAST协助确定冒口位置及尺寸,消除缩松及缩孔并保持高得料率,防止凝固冷却过程中偏析,尽可能减少铸造残余应力及铸件变形量。
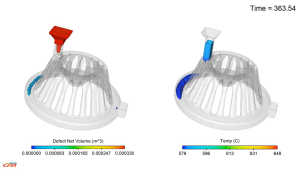
连续铸造
连铸工艺是生产半成品的常见工艺,连铸技术具有大幅提高金属收得率和铸坯质量,节约能源等显著优势。其工艺过程是将装有精炼好液态金属的浇包运至回转台,回转台转动到浇注位置后,将液态金属注入中间包,中间包或流槽再由水口将液态金属注入一个较短的,配有强冷的、带石墨衬板的结晶器中去。在结晶器末端出现稳定凝固结壳,在拉矫机与结晶振动装置共同作用以一定速度将结晶器内的铸件开始拉出,经冷却、电磁搅拌后,切割成一定长度的板坯。
在20世纪50年代引进连铸技术之前,钢水被倒入固定模具中形成铸锭。从那以后,连铸工艺得到广泛使用并发展到提高产量、质量、生产率和成本效率。
利用FLOW.3D CAST可以进行导流槽和中间包工艺优化以减少夹杂物;可以进行结晶器的设计优化,确定最优拉还速度和喷雾冷却参数,保证产品质量稳定:可以进行进口处注入条件优化及应力分布计算,保证应力符合相关标准。
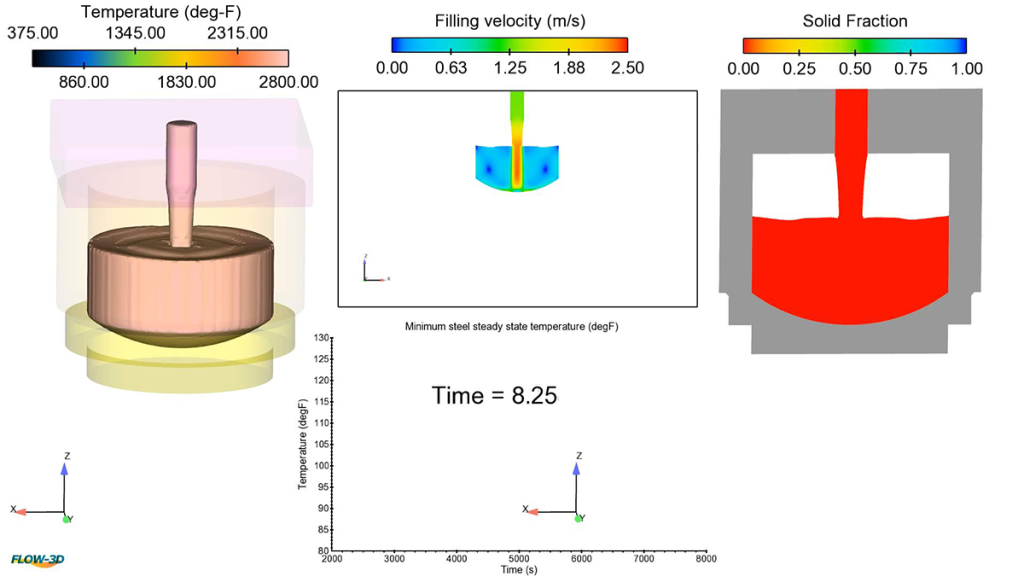
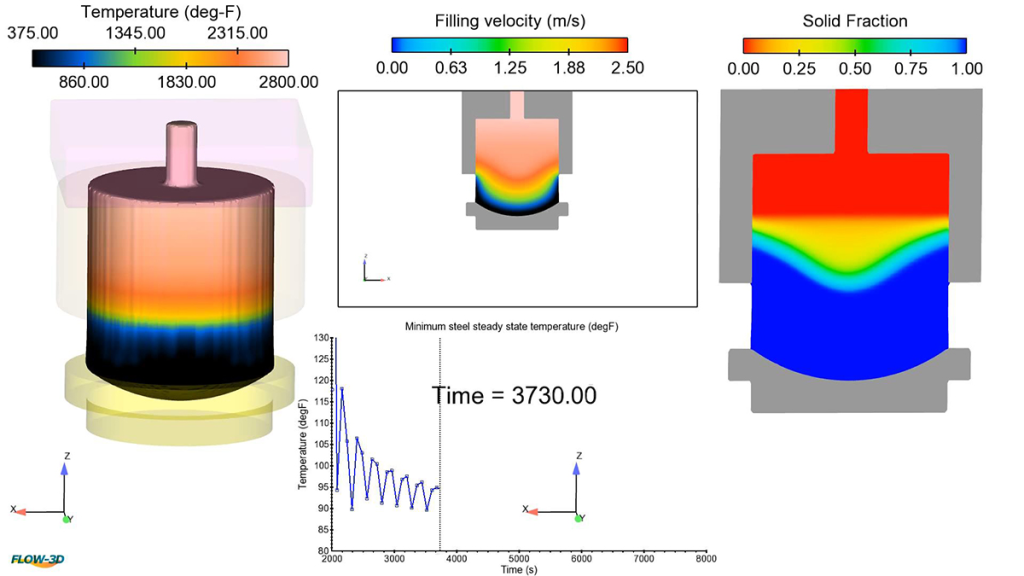
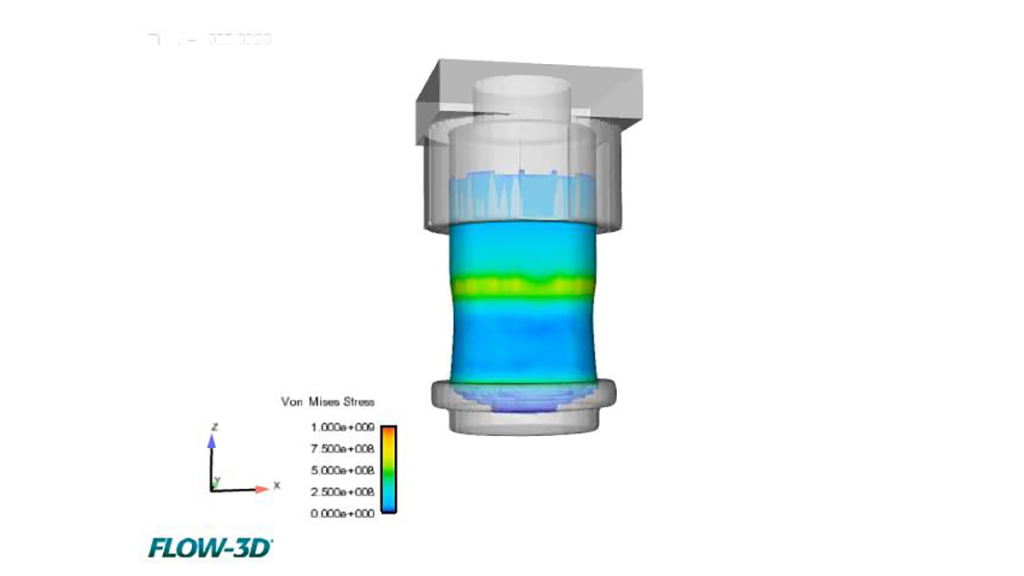
精密铸造
工艺亮点
- 流线化壳型生成工具,快速有效产生任意厚度壳模’
- 先进辐射计算模型,全方位考虑模壳表面之间辐射换热
- 先进多体运动控制,考虑复杂的布里奇曼法(Bridgman)、浇包运动及旋转运动等动力学
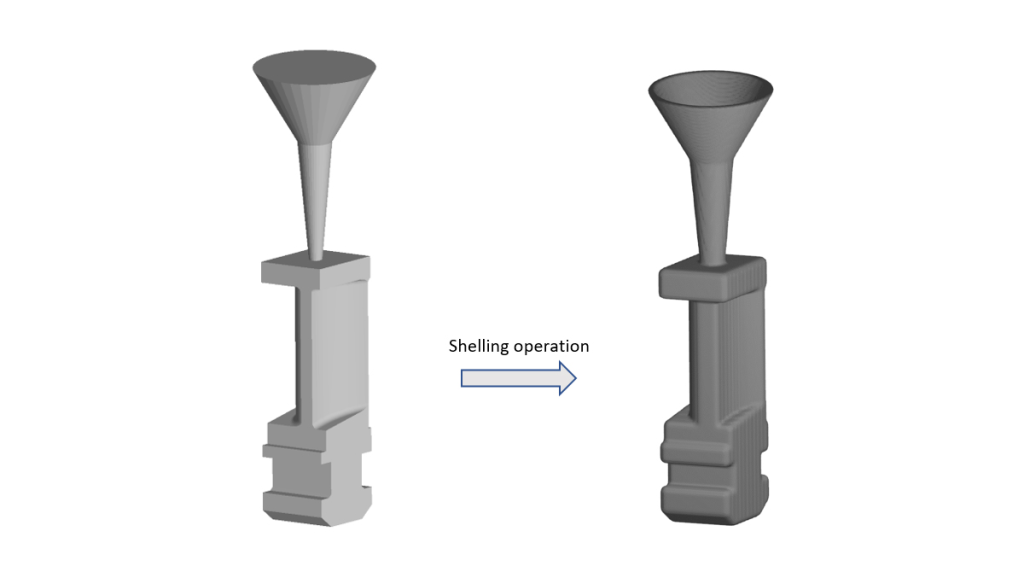

工艺概述
精密铸造工艺模块提供了一个易于使用的工具,可以考虑精密铸造中大部分的影响因素,包括模壳生成、浇注过程(静态或浇包运动),凝固及冷却过程(使用静态或模壳运动的布里奇曼法)。FLOW-3D CAST模壳工具提供了一种快速、 可靠的模壳几何生成工具,而全辐射和视因子模型能够准确地捕捉壳体不同部分之间的辐射换热。全新模块可以实现定向凝固工艺: 一个移动的烘箱,上 部分是加热的,下部分是冷却的,从而获得了布里奇曼(Bridgman)工艺。通过直观的后处理工具,可以更容易地评估熔体表面的演变过程、模具运动过程、填充流态细节及凝固方式,从而使工艺修改更有信心地实施。下图为定向凝固过程。
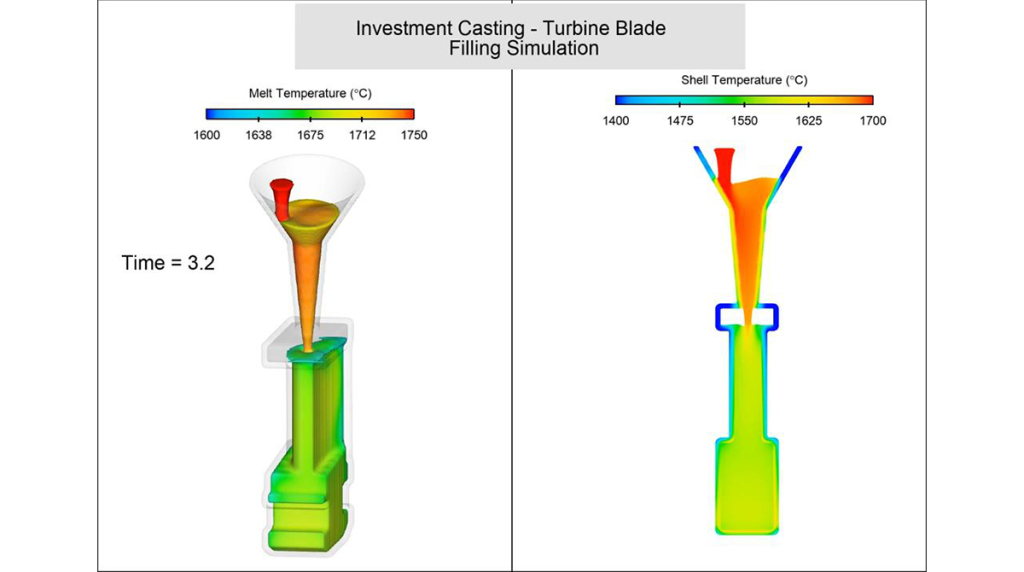
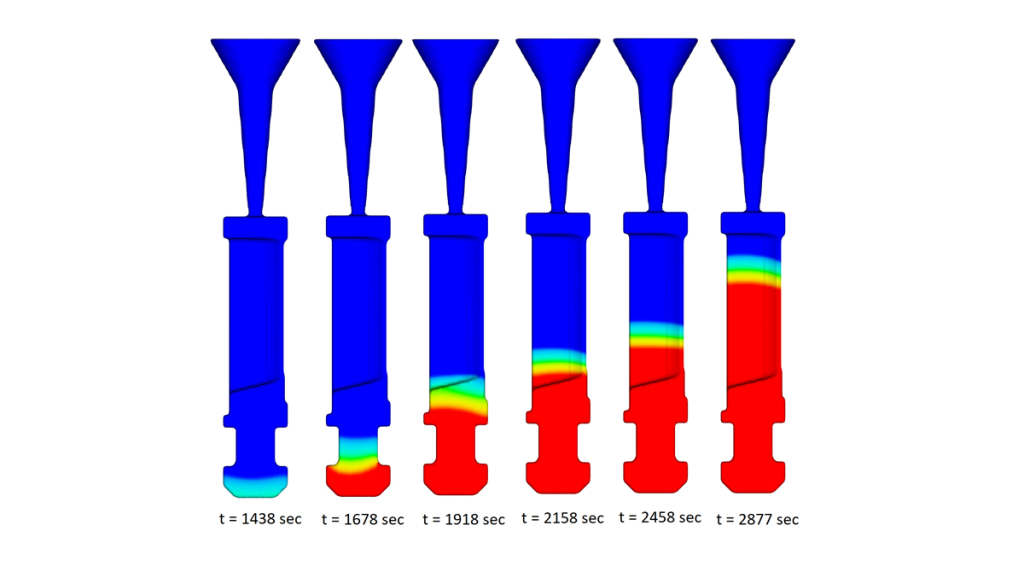
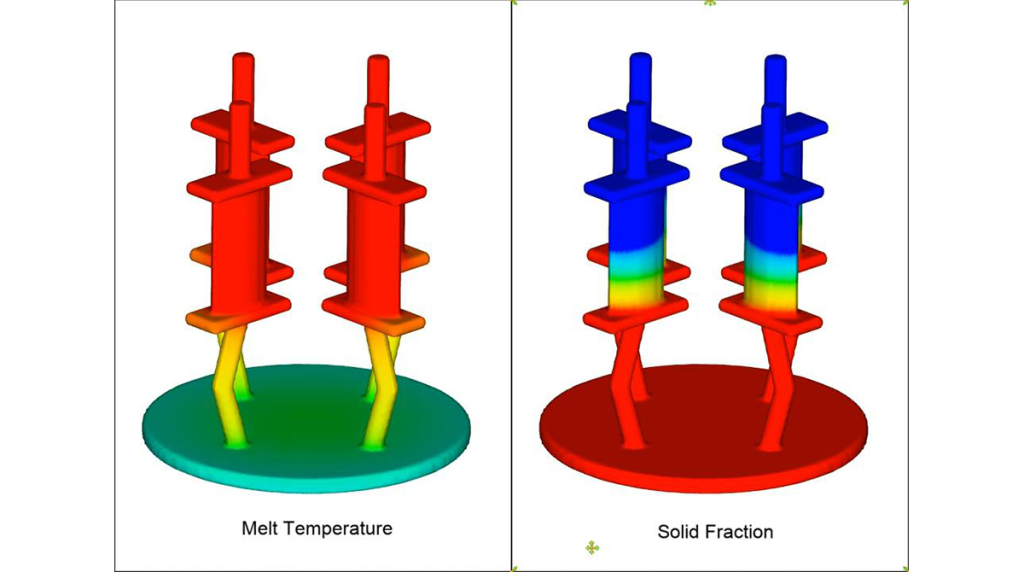