按需喷墨打印是一种有效的商业和消费图像复制方法。这项技术的原理也可以应用于功能印刷和增材制造领域。传统的喷墨技术已用于通过沉积和图案化从聚合物到活细胞的材料来打印各种功能性介质、组织和设备。这项工作的重点是将基于喷墨的技术扩展到 3D 实体金属结构的打印。目前,大多数 3D 金属打印应用涉及沉积金属粉末在激光或电子束等外部定向能源的影响下烧结或熔化以形成固体物体的情况。然而,此类方法在成本和工艺复杂性方面存在缺点,例如,需要时间和能源密集型技术在 3D 打印工艺之前制造粉末。
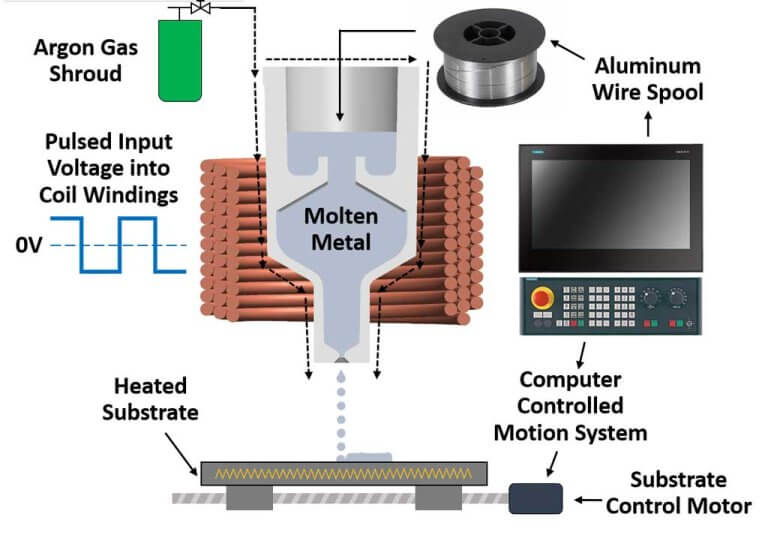
在本文中,我们将讨论一种基于磁流体动力学 (MHD) 按需喷射和液滴沉积在移动基板上的 3D 金属结构增材制造的新方法。为简单起见,该研究分为两部分:在第一部分中,使用 MHD 分析估计打印头内部的洛伦兹力密度产生的压力,然后将其用作 FLOW-3D AM 模型的边界条件用于研究液滴喷射动力学。在第二部分,FLOW-3D AM进行参数分析以确定理想的液滴沉积条件。
建模工作的结果用于指导设备的设计,如图 1 所示。一个线圈围绕着喷射室,并被电脉冲产生一个瞬态磁场,该磁场渗透到液态金属中并感应出内部闭环的瞬变电场。电场产生循环电流密度,它与瞬态场反向耦合并在腔室内产生磁流体动力洛伦兹力密度。力的径向分量产生压力,用于将液态金属液滴从孔口喷出。喷出的液滴行进到基板上,在那里它们聚结并凝固形成延伸的固体结构。可以使用移动基板逐层打印任意形状的三维结构,从而实现入射液滴的精确图案沉积。该技术已获得专利并由 Vader Systems 商业化,商品名为 MagnetoJet。
原型设备开发
Vader Systems 的 3D 打印系统的关键部件是打印头组件,该组件由一个两部分喷嘴和一个螺线管线圈组成。液化发生在喷嘴的顶部。下部包含一个亚毫米孔,其直径范围为 100µm 至 500µm。如图 1a 所示,水冷螺线管线圈围绕着孔腔(冷却系统未显示)。许多打印头设计的迭代开发一直在探索喷射室几何形状对液态金属填充行为以及液滴喷射动力学的影响。这些原型系统已成功打印出由普通铝合金制成的实体 3D 结构(图 2)。液滴的直径范围为 50 μm 至 500 μm,具体取决于孔口直径、几何形状、喷射频率和其他参数。
计算模型
作为原型设备开发的一部分,计算模拟在原型制造之前进行,以筛选设计概念的性能,即液滴喷射动力学、液滴-空气和液滴-基板相互作用。为了简化分析,开发了两种不同的互补模型,它们使用计算电磁 (CE) 和 CFD 分析。在第一个模型中,使用两步 CE 和 CFD 分析来研究基于 MHD 的液滴喷射行为和有效压力生成。在第二个模型中,采用热流体 CFD 分析来研究基板上液滴的图案化、聚结和凝固。
在 MHD 分析之后,从第一个模型中提取了等效压力分布,并将其用作 FLOW-3D AM模型的输入,旨在探索液滴喷射和液滴-基板相互作用的瞬态动力学。执行FLOW-3D AM模拟以了解孔口内部和周围的润湿对液滴喷射的影响。通过改变孔口内外的流体初始化水平,并允许脉冲之间有一个由脉冲频率决定的时间段,我们能够识别喷射液滴的特征差异,包括大小和速度。
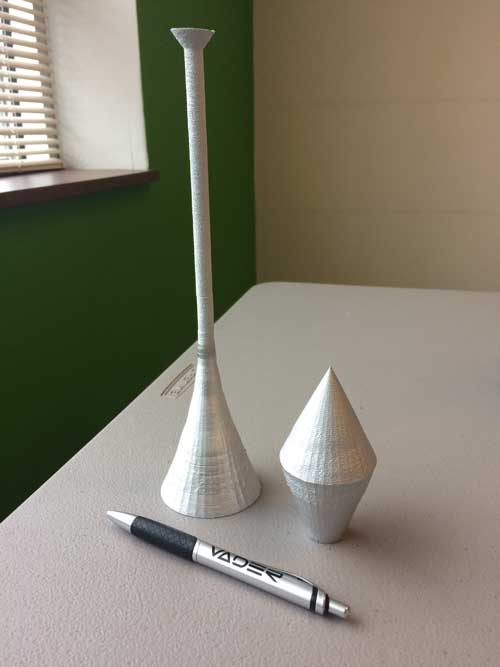
液滴生成
在 MagnetoJet 打印过程中,液滴以通常在 1-10 m/s 范围内的速度喷射,具体取决于电压脉冲参数,并在撞击基板之前在飞行过程中稍微冷却。控制基板上液滴的图案化和凝固的能力对于精确 3D 实体结构的形成至关重要。使用高分辨率 3D 运动底座可实现用于图案化的精确液滴放置。然而,控制凝固以创建具有低孔隙率且没有不需要的分层伪影的良好成型 3D 结构是一项挑战,因为它涉及控制:
- 当液滴冷却时,从液滴到周围材料的热扩散,
- 喷出液滴的大小,
- 液滴喷射频率和
- 来自已经形成的 3D 物体的热扩散。
通过优化这些参数,液滴将足够小以提供印刷特征的高空间分辨率,并且它们将保留足够的热能以促进与相邻液滴和层之间更平滑的聚结。应对热管理挑战的一种方法是将加热基板的温度保持在低于但相对接近熔点的温度。这降低了液滴与其周围环境之间的温度梯度,从而减缓了液滴的热量扩散,从而促进聚结和凝固,形成光滑的固体 3D 质量。
使用 FLOW-3D AM进行参数化 CFD 分析以探索该方法的可行性。我们对保持在较低温度下的基板运用Flow-3D AM进行了类似的分析,例如 600 K、700 K 等 据观察,虽然 3D 结构可以打印在较冷的基板上,但它们显示出不良的伪影,例如后续沉积金属层之间缺乏强聚结。这是由于沉积液滴中热能损失率增加所致。基板温度的最终选择可以基于给定应用的物体可接受的打印质量来确定。随着打印过程中部件变大,这甚至可以动态地进行调整以适应更高的热扩散。
液滴聚结和凝固
我们研究了加热基板上的层内液滴聚结和凝固作为液滴之间的中心间距以及液滴喷射频率的函数。在此分析中,液态铝的球形液滴从 3 毫米的高度撞击加热的不锈钢基板。液滴的初始温度为 973 K,基板保持在 900 K,略低于凝固温度 943 K。图 3 显示了当液滴分离距离从 100 变化到实线时,液滴聚结和凝固 μm 至 400 μm,步长为 50 μm,喷射频率保持恒定在 500 Hz。当液滴分离超过 250 µm 时,沿线出现带有尖点的固化段。在 350 μm 或更大的分离距离处,线段变得离散并且线具有未填充的间隙,这对于形成光滑的固体结构是不理想的。
我们对保持在较低温度下的基板运用Flow-3D AM进行了类似的分析,例如 600 K、700 K 等 据观察,虽然 3D 结构可以打印在较冷的基板上,但它们显示出不良的伪影,例如后续沉积金属层之间缺乏强聚结。这是由于沉积液滴中热能损失率增加所致。基板温度的最终选择可以基于给定应用的物体可接受的打印质量来确定。随着打印过程中部件变大,这甚至可以动态地进行调整以适应更高的热扩散。
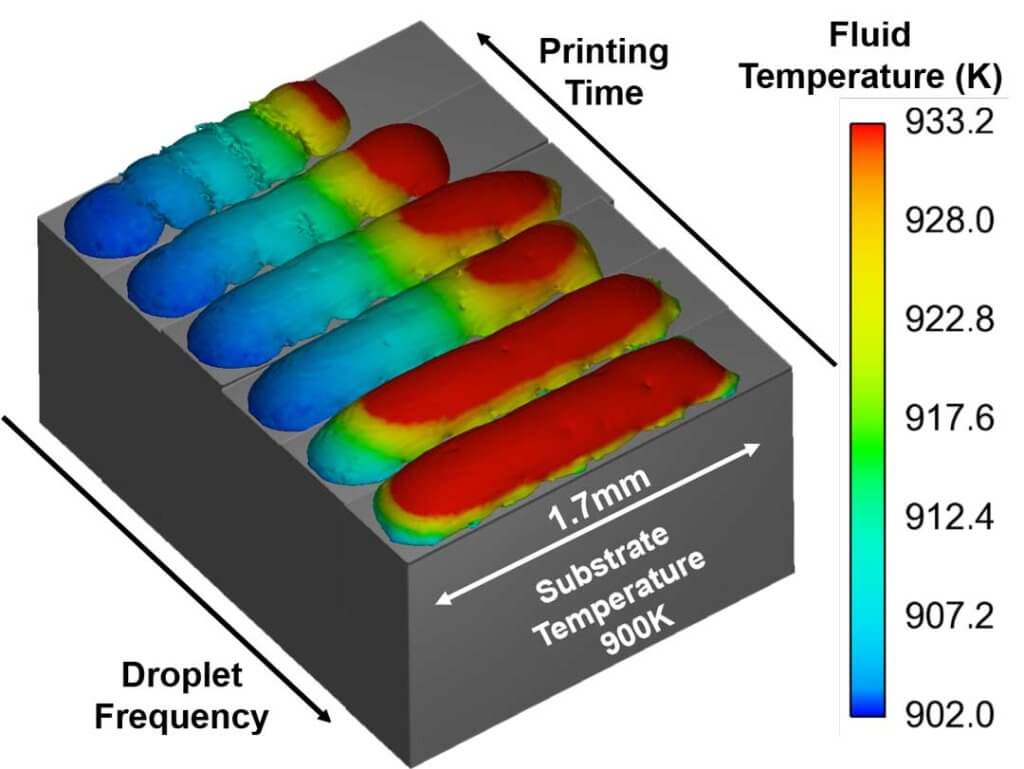
FLOW-3D 结果的验证
图 4 显示了印在加热基板上的杯状结构。在打印过程中,加热基板的温度根据打印部分的瞬时高度实时从 733K(430°C)逐渐升高到 833K(580°C)。这样做是为了克服随着物体表面积的增加而增加的局部热扩散。铝的高导热性使得这特别困难,因为必须快速调整局部热梯度,否则温度会迅速下降并降低层内聚结。
结论
根据Flow-3D AM的仿真结果,Vader System 的原型磁流体动力液态金属按需滴落 3D 打印机原型能够打印任意形状的 3D 固体铝结构。这些结构是使用亚毫米液滴的逐层图案沉积成功印刷的。仅使用一个喷嘴就实现了每小时超过 540 克的材料沉积速率。这项技术的商业化正在顺利进行,但在吞吐量、效率、分辨率和材料选择方面实现最佳印刷性能仍然存在挑战。新的建模工作将侧重于量化打印过程中的瞬态热效应、弯液面行为以及评估打印部件的质量展开。