现代铸造生产需要使用砂芯,而环保意识的日益增长以及更严格的法规为无机、无排放粘合剂系统的开发提供基础,系统中砂芯需要加热干燥和固化。在热芯盒法中,热量在芯盒中产生并传递到砂粘合剂混合物中。然而,热芯盒法表现出两个主要的技术缺点。
第一个缺点是石英砂的导热率非常低,约为 1 W/(m·K)。由于由外向内传热,该过程非常耗时,可能导致截面硬度过高并因此产生质量问题。出于这个原因,应用高达 523.15 K 或更高的芯盒温度来加速热传递。热芯盒法的第二个缺点是砂芯干燥本身不能直接测量和实时数字化。相反,它只能通过记录外围参数来被动测量。
ACS 砂芯工艺流程
新的专利先进砂芯解决方案(ACS)工艺旨在实现节省时间和节约能源的砂芯干燥和固化。ACS 工艺具有所有无机粘结剂体系的共同特性:以水为基础能够导电。关键因素是开发导电芯盒材料,其导电性可调整到砂-粘结剂混合物的导电性。当施加电压时,电流均匀地流过芯盒和砂粘合剂混合物,如图 1 所示。
更准确地说,电流通过砂粒之间的导电粘结剂时由于其固有的电阻,砂芯均匀加热而不形成加热不均产生的高硬度截面。这是基于焦耳第一定律的欧姆加热。在串联过程中,导电芯盒通过这一定律加热,能加速干燥过程。这是另一个重要的优势,因为对于ACS工艺,不再需要芯盒内复杂的加热设备,从而简化了芯盒的构造。
借助这一新工艺,热量首次直接作用在砂芯中。由于必要的热量通过均匀分布的粘合剂产生并传递到相邻的砂中,石英砂的低导热率不再是限制工艺因素。此外,电气参数首次能够进行全面的实时监控,并记录干燥全过程。使用 FLOW-3D,可以模拟 ACS 过程,量化过程的收益,满足工业应用的重要标准。
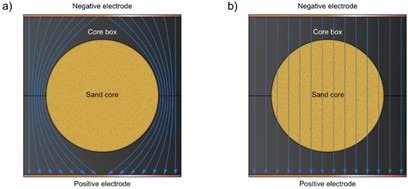
实验设计及结果
该实验模型基于 Starobin 等人的工作,但使用FLOW-3D 中的机电模型对其进行了扩展。以下研究集中于不考虑吹扫(purging)的单流体模拟。
第一步,使用无机砂粘合剂混合物对模拟模型进行实验研究和验证,以研究加热和温度相关的导电率。测量了达到 373.15 K 所需的时间以及输入砂芯的功率和能量。根据实验分析结果,建立了一个基本的仿真模型。出于谨慎考虑,基本结果仅以定性方式呈现。结果如图 2 所示,表明测量值与模拟值高度一致。

基于验证的结果,ACS 工艺和模拟使用简单的大容量几何图形显示,与热芯盒法相比,它说明了 ACS 先进工艺开发的基本原理和巨大潜力。几何对齐可以从图 3 中得到。
模拟了三种情况:(1)热芯盒法过程;(2) 使用冷工具 (293.15 K) 的 ACS 冷启动过程;(3) 考虑到焦耳效应导致的工具加热的 ACS 系列过程。所有三维模型均以 1 mm 的单元尺寸离散化。表 1 总结了计算方案的最重要细节。
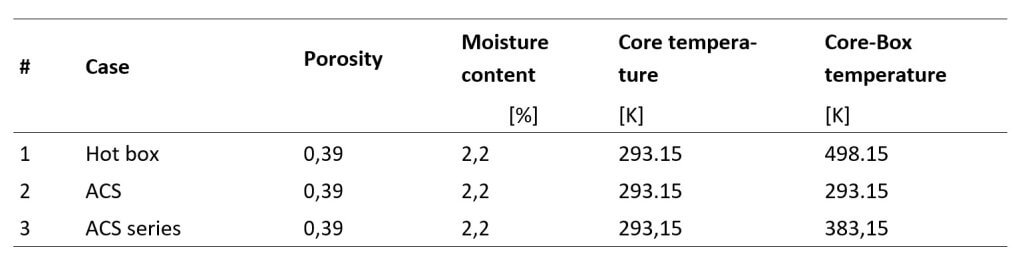
结果与讨论
图 4 显示了热芯盒法的温度和水分变化,清楚地显示出由外而内的热传递和相应的水分减少过程。
模拟进行了 120 秒,模拟结束时砂芯中心仍存在水分;在实践中,循环时间的设定提前终止了干燥过程,此时砂芯由于不均匀的加热形成了壳,砂芯中心残留水分。