使用3D扫描来评估涡轮机的状况和效率、检查其形状、创建副本、扫描新的涡轮机是否合格等已经在多个水力发电厂中成功进行,而三维扫描系统和手持3D扫描仪TRITOP也可以对大型复杂部件(如水轮机)进行高精度测量,通过拍照式三维扫描仪TRITOP详尽的3D模型可以检测到与转子理想几何形状的最轻微偏差。
我们的合作伙伴 TOPOMATIKA 已成功与克罗地亚土木工程学院和克罗地亚电力行业合作,经过团队的努力,在使用3D扫描后几台水力发电厂的涡轮机被数字化后创建了各种 3D “建造”,这些 “建造”数据被用以提供“建造与设计”,并按照涡轮及检测要求的设计形成检查报告,以帮助评估涡轮机的状况和效率。同时,3D 扫描数据还能用于创建重复组件并设置基线以生成新设计。而非接触式 3D 光学数字化系统有助于对简单和复杂物体进行准确和详细的扫描,结合3D扫描成像仪TRITOP的数字摄影测量系统,可以快速准确地扫描从喷气推进到地面发电涡轮机到全尺寸飞机的物体,这一测量系统便捷、易于运输,并且能够支持现场3D扫描(在发电站、车间等)。也就是说,使用便携式3D扫描系统,不再需要将物体带到测量实验室。
Pelton 涡轮转子的 3D 扫描
冲击式水轮机用于水压高、水量少的水力发电厂(图 2)。由于这些水轮机以极快的速度运行,转子的几何形状和稳定的旋转是关键的性能标准。转子的3D数字化从使用手持专业级数码相机的数字摄影测量 (TRITOP) 阶段开始(图 3)。三维立体扫描仪TRITOP软件处理获取的会话图像,并自动计算应用于涡轮机转子和叶片的参考标记的准确位置。
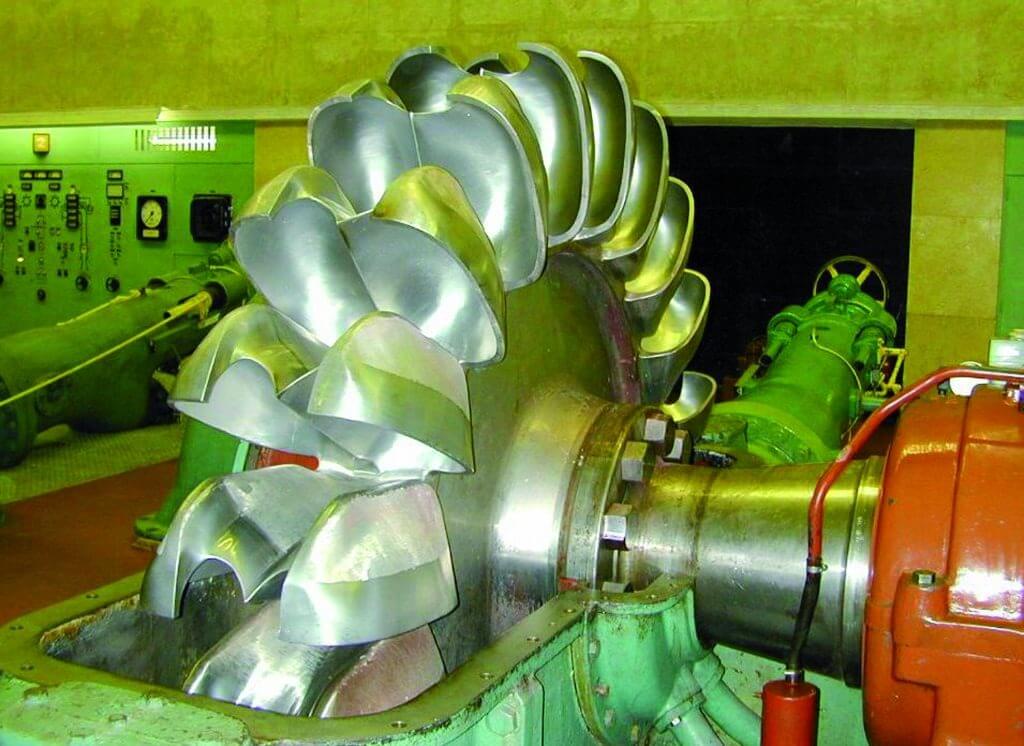
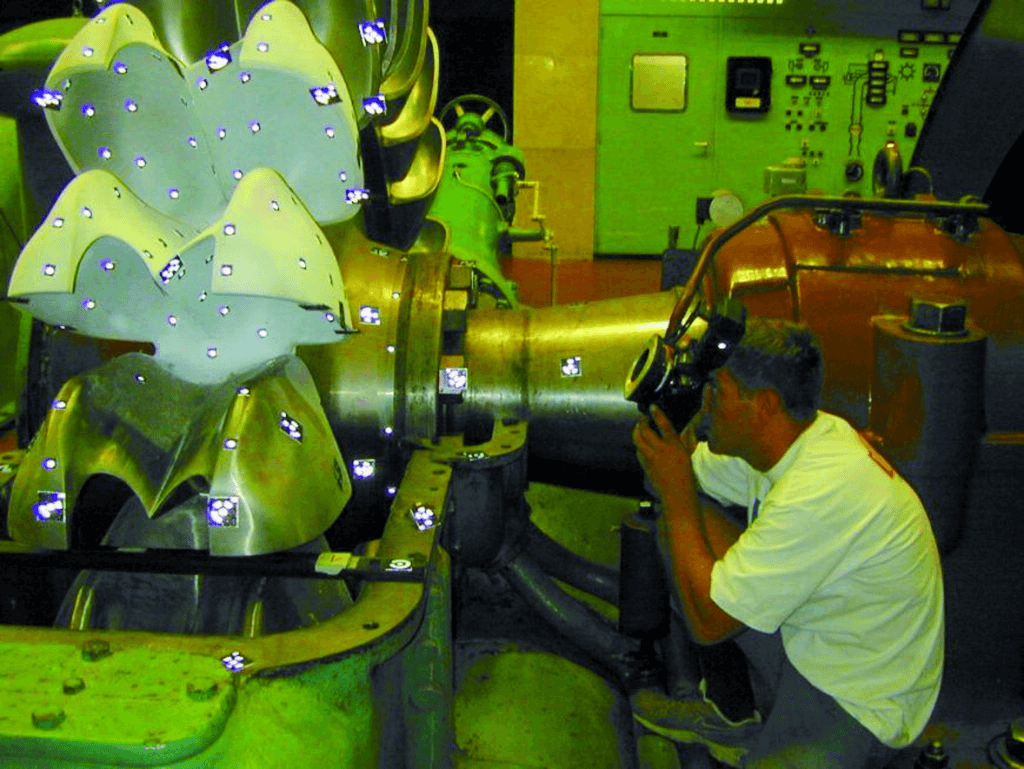
3D扫描系统在物体表面投射出密集的条纹图案。这些图案由双数码相机记录、处理并产生代表对象该区域的扫描数据(点云)。在扫描过程中,系统还准确地定义了测量区域中可见的参考标记的中心。基于这些参考标记的独特方向,扫描数据补丁会自动准确地合并在一起。根据 3D 扫描系统配置的不同,每次扫描需要 1 到 7 秒,每次扫描最多可生成 400 万个 3D 测量点,通过这种方法,可以快速准确地获取和验证叶片的形状。重复此扫描过程,直到涡轮转子叶片的各个角度都成功数字化。在 Pelton 涡轮转子中,各种根据 TRITOP 三维数字拍照扫描仪的会话创建的全局参考标记位置文件自动合并在一起。图 4 则显示了数字化转子的阴影 3D 测量数据,其中生成的数据文件由数百万个 3D 点组成,详细描述了每个叶片的形状。其分辨率(点密度)约为0.3 毫米(0.010 英寸)。如果需要的话可以轻松调整 3D 扫描系统以提供高分辨率或更大的测量范围。
这种详细而准确的 3D“原版”数字化模型的好处是可以检测到与转子理想几何形状的最轻微偏差。扫描的涡轮叶片数据可以与 CAD 模型(如果有)、其他叶片的数据进行比较,或者为了对称性检查,可以镜像数据,见图5形状上的偏差用不同的颜色表示,对应于图像右侧的刻度。涡轮叶片形状偏差高达 2 毫米(0.08 英寸)的区域清晰可见(红色和深蓝色区域)。根据要执行的任务以及下游处理软件和系统的能力,还可以显示和导出具有较少测量点(细化数据集)或截面数据的结果(图 6)。