金属成型的光学3D检测
设计&模拟篇 -设计
3D 数字化有助于快速生成和有效使用 CAD 数据。
- 实际的 3D 坐标可以对模型、零件和工具进行逆向工程。因此,要对这些对象的 3D 几何形状进行全面扫描,然后通过表面重建将其转换为 CAD 数据。
- 可以有效地进行零件检测。在设计过程中,CAD 数据直接提供检测功能。零件一生产出来,就可以立即进行检查。
- 光学测量系统将全自动的在完整的实际 3D 坐标和 CAD 数据之间测量全场偏差。
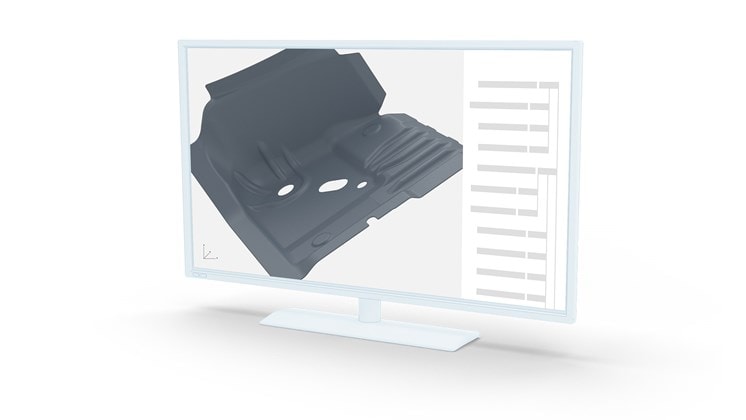
模型、零件和工具的逆向工程
使用 ATOS 进行全场几何采集可以在现有 CAD 软件包中对模型、零件和工具几何进行表面重建和调整。
挑战
在某些情况下,需要扫描物理模型、零件或工具的 3D 几何形状以创建相应的 CAD 数据。
例如,在汽车行业,设计师用橡皮泥将新车的外形设计为物理模型。这些设计模型必须转换为数字数据,以便设计人员可以继续在 CAD 程序中对其进行处理。
另一个挑战是再制造或维修不存在设计图纸或 CAD 数据集中有旧的或有缺陷的零件和工具。这是基于 CAD 设计的。因此,这里也需要这些部分或形状各自的几何数据。
解决方案
ATOS 使之成为可能:ATOS 系统可实现对真实物体的快速全场扫描和几何采集。由此产生的测量数据构成了通过多边形化和表面重建(逆向工程)创建这些对象的 CAD 数据的基础。
扫描对象及其几何图形时,工程师可以将 CAD 软件包中的 3D 几何图形作为 CAD 模型进行处理。
好处
- 精确的模型、零件和工具的3D形状的全场采集
- 标准几何形状和自由曲面的表面重建
- 在模型设计外形中从想法到产品的更快过度
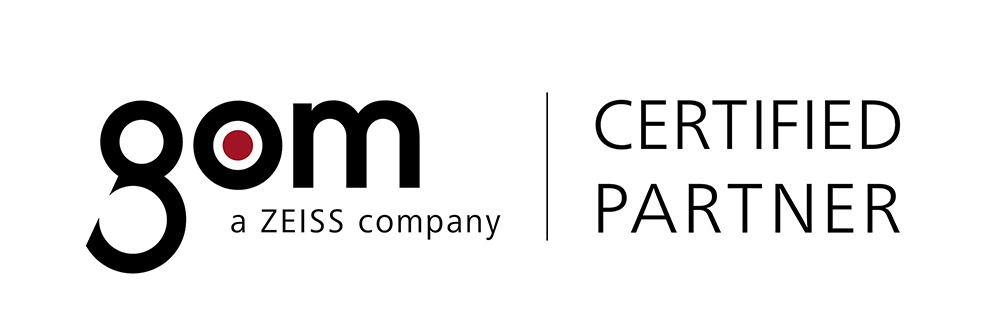
金属成型的光学3D检测
设计&模拟篇 -模拟
产品和制造过程采用数值模拟方法进行设计和优化。这些模拟的结果能尽可能地提供足量信息。
金属成形过程模拟的一个重要因素是所用金属的材料特性。材料特性会影响零件的变形行为,从而影响模拟计算的准确性。
使用 ARGUS 系统,可以根据实验测量检查和优化成形模拟。
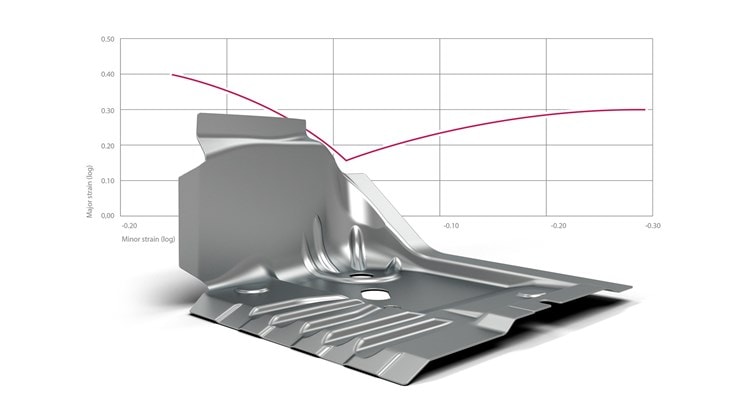
GOM 光学检测
挑战
产品和制造过程采用数值模拟方法进行设计和优化。这就提出了一个问题:这些模拟的结果有多精确?许多因素在这里起作用。除此之外,材料特性会影响零件变形行为以及模拟计算的准确性和可靠性。
成型模拟可以通过实验测量来验证和优化。为此,用户使用 ARGUS 系统测量零件。然后,可以将这些测量数据在整个零件表面上与相应的 FEM 计算进行数值比较。分析了与模拟数据相比,实际零件几何形状、材料厚度减少以及主要和次要应变的表现。
这些发现可以反馈到下一次模拟的参数化中。这样可以进一步改进计算并降低未来项目的开发成本。
GOM 光学检测
GOM 光学检测
全场对比
有限元模拟结果与零件测量
优化
提高可靠性的模拟
降低成本
通过建立测量数据不断改进