用于钣金加工的大型工具或模具大多是从铸造坯料中铣削出来的。 毛坯必须有多余的材料来补偿嵌入和铸造中的偏差。 此外,坯料在活动区域中必须有过多的材料,以允许对工具进行加工和手动调整,以确保在冲压过程中产生所需的零件形状和表面质量。
坯料的数字化可以通过我们的 3D 扫描解决方案完成。 在本例中,我们使用3d激光轮廓扫描仪 ATOS Q ,导出数据可以直接导入 CAM 系统。 根据实际数据,毛坯的形状现在可以适合所需的模具几何形状。 然后可以用最小化的处理时间来定义最佳拟合。
此外,可以计算出最优且无碰撞的切削路径,以理想的切削参数和最短的切削时间,以可预测、快速、节省和无人操作的方式从毛坯生成刀具。
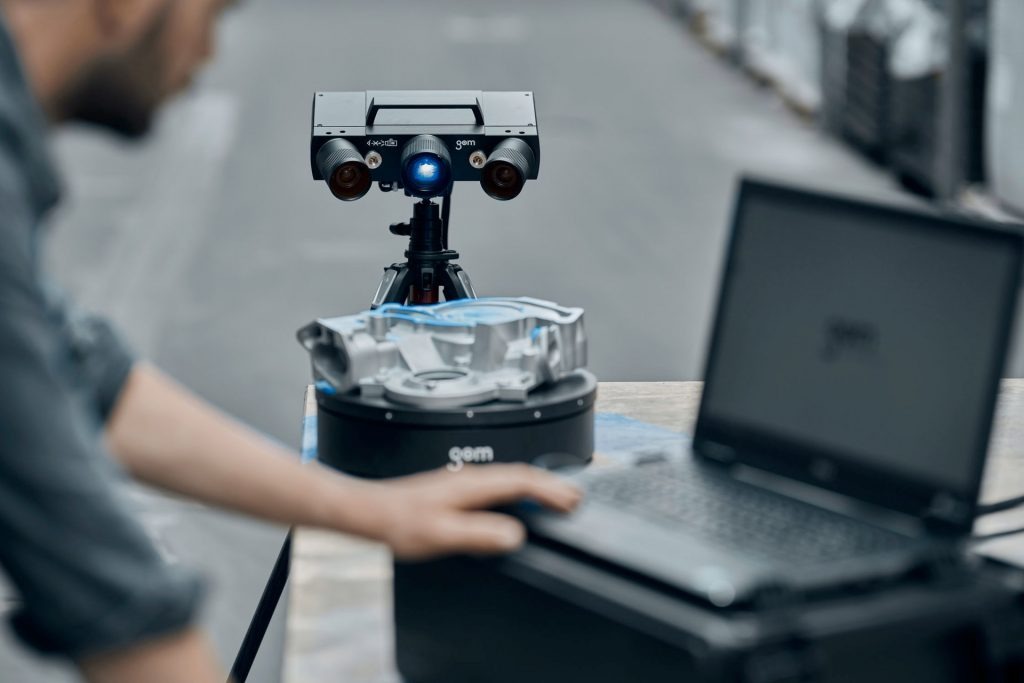
用于钣金加工的大型工具或模具大多是从铸造坯料中铣削出来的。 为了生产这些毛坯,使用易于加工的材料(Styropor 或类似材料)构建模型。 然后添加与铸造相关的附加项,例如入口和出口。 然后将模型嵌入铸砂中。 背模后,将模型材料烧掉,制成铸件。 毛坯必须有多余的材料来补偿嵌入和铸造中的偏差。 此外,毛坯在活动区域中必须有过多的材料,以允许对工具进行加工和手动调整,以在冲压过程中产生所需的零件形状和表面质量(图 1)。
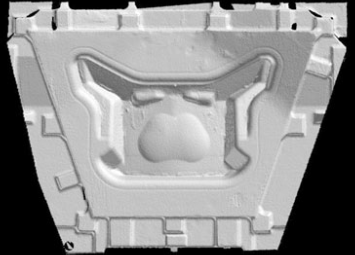

对于加工,将坯料对齐并用螺栓固定在适当的大型卧式铣床的工作台上。首先通常将底部加工成一个平面,然后车削毛坯,并且可以看到工具的粗略轮廓。由于在铣床上加工毛坯的时间是一项主要成本,因此减少时间是非常常见的方式。因此,在将其定位到铣床上之前,通常会检查大坯料并在坯料上手动应用对齐标记。根据标记,将毛坯定位在铣床上,对齐并用螺栓固定。
借助工业三维激光扫描仪 ATOS Q “背投影”的 pro line 功能,这些标记可以实时投影到零件上。然后,通常通过手动控制将其切断或铣削来去除铸造特定的修改。然后定义铣刀和毛坯的第一个接触点,让刀具在空中工作,同时小心地手动接近毛坯。从这个起点开始粗加工。由于切削深度不均匀且CAM软件无法预测,因此必须使用缓慢的进给速度,并进行人工监督和修正。
基于使用手动卡尺进行的测量,不可能对大而复杂的毛坯进行安全或优化的对齐。错误的对准甚至可能要求沉积焊接能够加工未来工具的所有相关表面。对于坯料的数字化,蔡司在三维扫描设备 ATOS 上增加了一个大的测量区域。对于大型铸造坯料的数字化,在坯料上应用标记。然后捕获中心视图。然后捕获额外的视图并自动传输到现有的扫描数据中。基于这种技术,最大尺寸为 5 x 3 米的坯料可以在一小时内进行数字化,同时保持要求的精度。
自动化三维扫描仪ATOS 系统的导出数据要么是“stl”格式的文件,要么是节数据。通过使用蔡司逆向工程软件,我们还可以创建 CAD 文件。 ATOS 导出数据可以直接导入 CAM 系统,例如 TEBIS(“SCAN”模块)或 WorkNC(Sescoi Inc 的“NCSpeed”模块)。根据实际数据,毛坯的形状现在可以适合所需的模具几何形状。然后可以用最小化的处理时间来定义最佳拟合。
此外,可以计算出优化且无碰撞的切削路径,以理想的切削参数和最短的切削时间,以可预测、快速、节省和无人操作的方式从毛坯生成刀具。 在德国的 BMW、Mercedes 和 Audi 与 TEBIS 和 SESCOI 合作使用的是上述工艺。 在实际情况下,在铣床上的时间可以从 48 小时减少到 8 小时。 对客户而言,重要的是,除了节省时间和金钱之外,可靠、节省和可预测的过程。
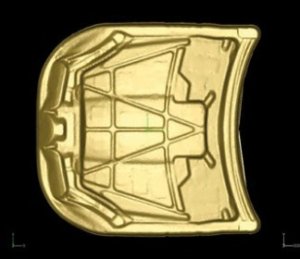
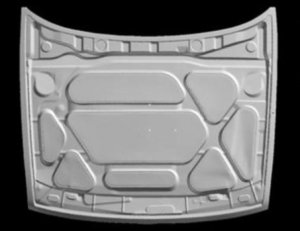
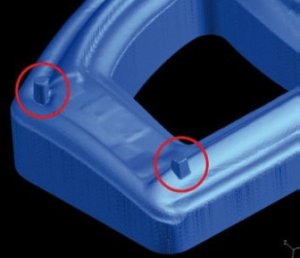
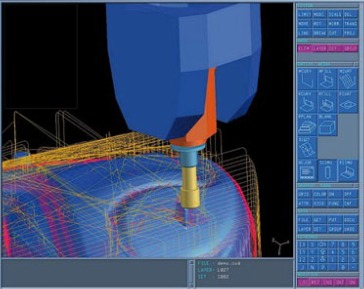
汽车客户开始要求准备好使用的工具,并从他们的供应商那里获得对实际工具形式的数字描述。 基于这些数据,可以启动质量控制和可追溯性过程。 磨损可以量化,工具的返工可以订购并使用明确定义的主表格进行测试,如果需要,可以快速生成工具的准确副本。 扫描仪也可用于扫描此应用程序的工具。 为了获得所需的高精度,3d扫描成像仪ATOS 被校准以数字化较小的测量区域。 标记附在工具上,摄影测量用于定义该标记的准确位置。 然后使用传感器扫描工具并将数字化数据插入由标记定义的网格中。 使用 ATOS 技术,可以保证百分之几毫米的扫描数据精度。
ATOS 传感器是设计、产品开发和质量控制中数字化的标准。 ATOS 扫描仪中使用的两个相机在每次测量中验证扫描仪的校准,因此是在质量控制应用中使用便携式系统的必要条件。 此外,用户可以在几分钟内完成基于认证工件的校准更改测量区域。 利用这种潜力,ATOS 可以根据不同的客户需求进行调整,并提供准确高效的结果。