用于重力铸造的创新型浇口系统
- 砂模铸造
- 低压压铸
- 重力压铸
- 高压压铸
- 消失模铸造
为每种情况选择最合适的铸造工艺取决于:
- 发动机概念/产量
- 技术要求
由于特定的产品要求,重力压铸专门用于柴油发动机的气缸盖和曲轴箱
铸造专家尝试改进标准重力压铸工艺:
- 减少铸造缺陷
- 更高的铸造质量/更好的机械性能
- 填充过程中的最小湍流
- 无需浇注盆(减少填充过程中的湍流)
- 无需流道系统(减少开发工作)
- 夹带空气风险低
- 氧化物残留在钢包内
- 任何氧化物夹杂物的风险低
- 充满热材料的立管(良好的喂养)
- 底板可以在整个过程中冷却
- 填充工艺(更好的机械性能)
- 不适用于每个铸件
- 填充过程开始时出现一些湍流
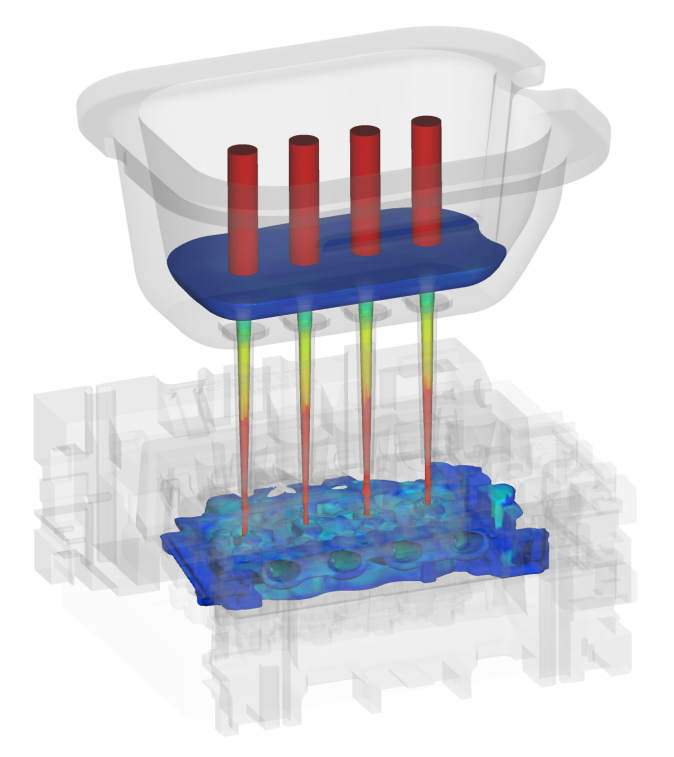
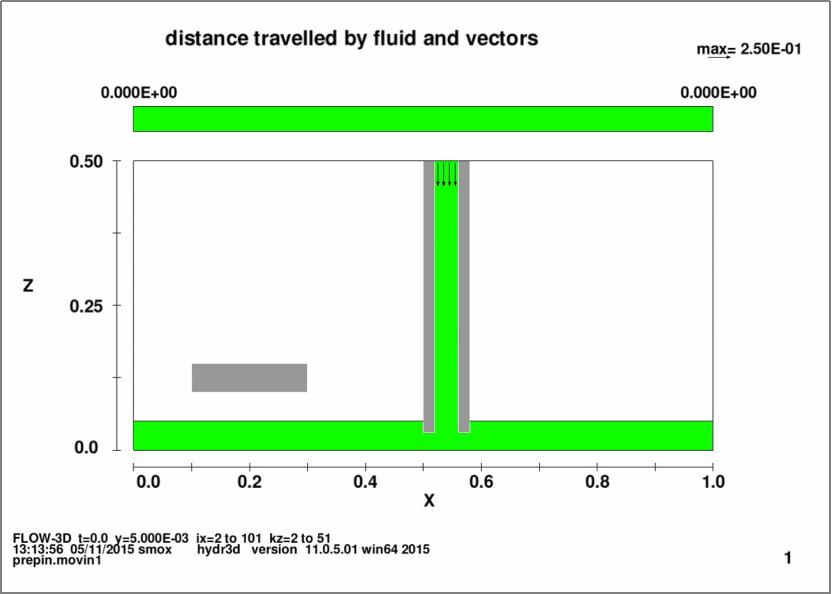
- 填充行为(湍流,速度,…)
- 喷油器中的流体流动
- 温度分布(钢包、型腔、注射器……)
- 可能的铸造缺陷(氧化物、气泡……)
- 工艺参数(温度、时间……)
- 塞子的移动方式
- 钢包移动方式
- 塞子和钢包的设计
- 喷油器设计
- 实验工作量大大减少
使用无机粘合剂系统的砂芯吹芯和干燥
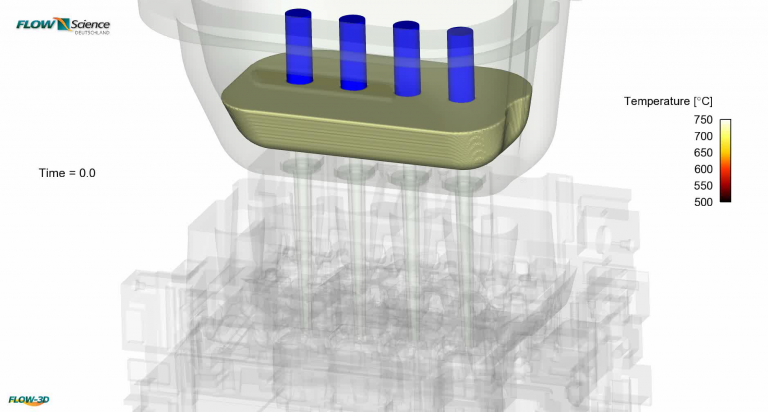
宝马工厂的轻金属铸造厂于 2010 年推出了一种新的重力压铸砂芯生产方法——传统的有机粘合剂被高度环保的无机粘合剂取代
环境方面:
- 几乎没有污染物排放(燃烧残留物的排放量减少了 98%)
- 工作条件显着改善
- 经济和人体工程学优势:
- 由于减少了芯气,提高了铸造质量
- 生产和降低工具温度
- 所得轻合金部件的强度提高(由于更快的凝固)
“宝马的兰茨胡特工厂是世界上第一家完全无排放砂芯生产的铸造厂。”
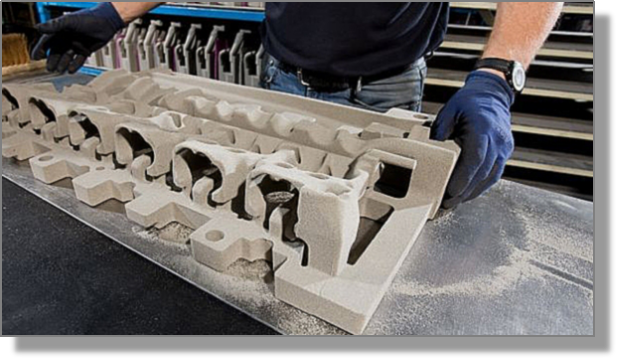
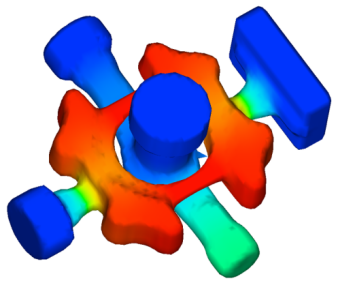
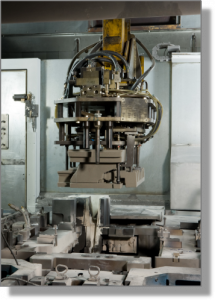
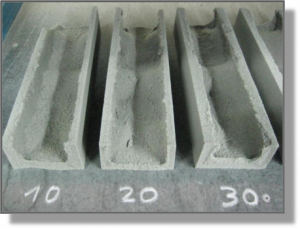
工艺步骤:
将型砂(含粘合剂)射入加热的模具中(使用射芯机)
芯子用热加压空气干燥(核心首先在靠近墙壁的薄层中干燥和硬化)
核心内部的水被热空气蒸发(水会在较冷的地区凝结)
空气-蒸汽混合物通过排气喷嘴离开堆芯
水的去除导致芯部硬化(粘合剂的化学反应)
新工艺的引入需要大量的实验
沙子特性的测量(粘度、孔隙率、粒度……)
吹制工艺(填充行为、工艺参数……)
干燥过程调查(方法、设备、工艺参数……)
新型芯干燥模型(软件)的开发
- 模拟有助于理解过程
- 不同干燥方式的比较
- 工艺参数研究
- 工具(加热系统、喷嘴、通风口等)和设备的优化
- 大量减少实验
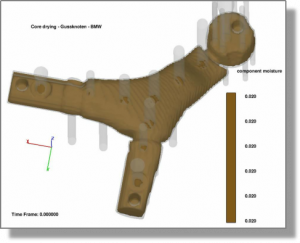
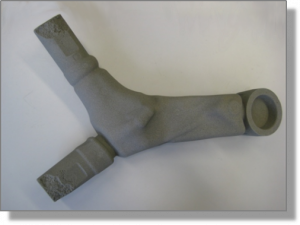
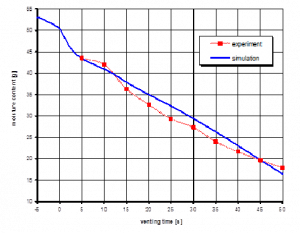
盐芯在高压压铸中的应用
- 汽车行业呼吁:
降低成本
整体设计(减少部件数量)
更高的生产力 - HPDC 中的底切
仅适用于复杂的滑块(高维护)
技术在经济上不适用
- 重力铸造砂芯不适合应用于 HPDC:
- HPDC工艺的高压和高速度强度不足
- 失核技术:
开发完整的新组件的可能性
生产中空零件和复杂的内部设计(底切)
功能集成度高
减少加工、密封和组装工作
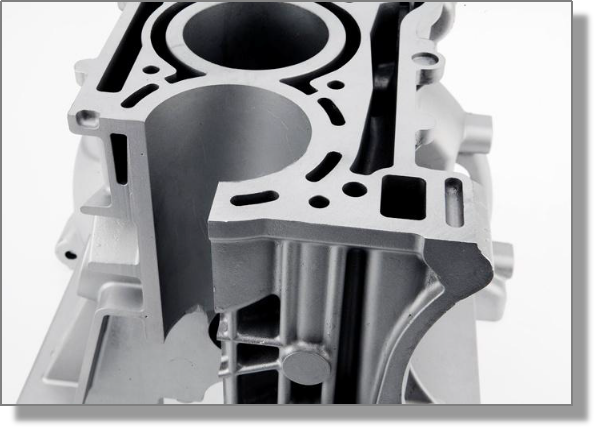
未知的新技术
- 材料特性
合理的工艺参数(生产和使用)
盐芯的生产
工艺类型(重力铸造、HPDC……) - 工艺参数
盐芯质量/缺陷(表面、缩孔……)
盐的固化(密度变化非常大) - 盐芯的使用
铸造过程中的高动态力
由于高内浇口速度导致的核心故障
应力导致的核心裂缝(由于温度梯度)
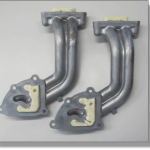
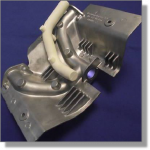
支持开发盐芯用途的模拟
工艺研究(收缩行为,……)
工艺参数的确定
大量减少实验
模拟盐芯生产
填充行为
– 可能的缺陷
– 浇注和通风系统的设计
凝固收缩过程
– 表层快速凝固
– 密度变化大
– 收缩系数取决于零件几何形状
– 表面是绝缘体
– 中心区凝固时间长
– 收缩孔
– 应力(可能的裂缝)
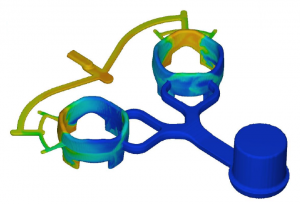
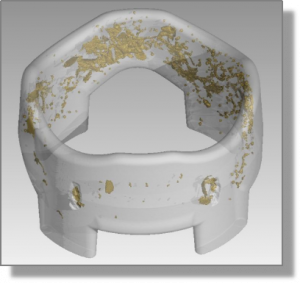
铸造过程中盐芯使用模拟
- 充填固化工艺
- 由于高内浇口速度导致的核心故障
- 允许模拟熔体和盐芯的相互作用
- 填充过程中芯部受力的调查(由于应力导致芯部破裂)
- 热致残余应力
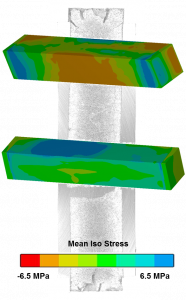
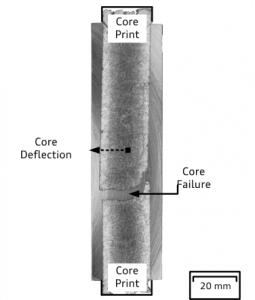
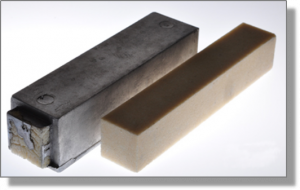
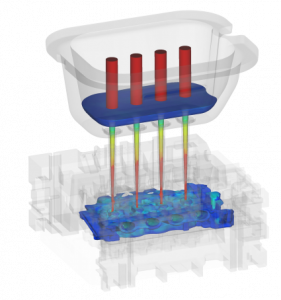
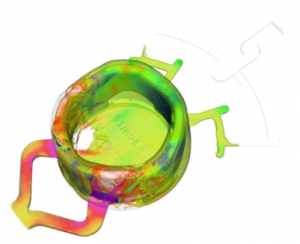