快速安全地铣削工具
如果使用 ATOS 系统对坯料进行数字化处理,则可以更快地铣削由铸造坯料制成的成型工具。基于此数据,CNC 机床的运行时间可减少50%之多。
- 在数字化铸坯的基础上快速安全地铣削工具。
挑战
较大的成型工具由铸坯制造。如果要铣削工具的铸坯已经数字化,则这种工具的 CNC 生产可以更快地完成。
解决方案
用户使用 ATOS 系统扫描毛坯,提供坯料的 3D 模型。之后可以将毛坯的几何形状与 CAD 模型进行比较,并识别任何尺寸偏差。然后,他确定测量数据中的加工余量,并将其作为参数传输到铣床。测量数据还有助于在铣床上快速、最佳地对齐铸坯。铣削后,用户扫描铣削结果并将其与标称数据进行比较,以便进行所有必要的返工。
铸坯也经常具有干扰轮廓,例如浇口。这些可以在毛坯轮廓的 3D 模型的早期阶段检测到。检测到的信息可以控制铣刀,从而在铣削过程中不会与毛坯发生碰撞。
结论:以 3D 扫描铸坯有助于确定最佳铣削路径,避免耗时的“空气铣削”并防止加工工具断裂。
好处
- 运行时间减少为数控机床的50%;
- 由于铣刀与毛坯碰撞而导致的加工工具没有昂贵且耗时的破损;
- 最佳控制铣削结果
快速工具试用
试模时,必须检查试模件是否符合设计要求。使用 ATOS 系统,可以对零件进行全面扫描和分析。
- 使用数字化试模零件快速试模
挑战
制造工具后,有必要检查用它生产的零件在多大程度上满足设计要求。
解决方案
ATOS 系统使用户能够在试模期间直接在冲压厂现场对零件进行全表面 3D 数字化。这使用户可以非常快速地识别试模零件的实际几何形状与 CAD 模型之间的偏差。此外,通过易于理解的图形画面检查功能尺寸、回弹、修边、偏转和试模零件的孔图案。
通过将测量数据与试件的 3D 模型进行比较,可以快速轻松地评估以下内容:
- 该工具的工作正确性如何?
- 哪些部分仍需要更改?
好处
- 在试用期间对零件进行全流程易于理解地分析;
- 将零件几何中的问题区域及时本地化;
- 无应力安装的装配精度和满足光学的要求确保正确的几何形状
基于光学测量数据的工具校正
工具试模旨在尽可能快地迭代生产成品工具,以便生产出正确的零件。如果使用 ATOS 系统对工具和试模零件进行数字化,则可以获得工具校正的精确数值。
- 基于光学测量数据的工具校正
挑战
工具试模就是尽可能快地迭代生产成品工具。一种工具,在材料、工具和压力机的复杂相互作用中,生产出满足设计要求的精确零件。
解决方案
通过使用 ATOS 系统对工具和试模零件进行数字化处理,用户可以获得校正值。他可以使用这些值来修改设计以及对工具进行特定调整。
这些信息告诉用户零件的几何形状与 CAD 模型的偏差在哪里,以及这些偏差在哪里变得太大。它们帮助用户分析回弹并精确确定其补偿。它们还提供有关如何调整孔图案和修整的数据。
好处
- 快速工具和流程优化
- 在工具开发中更少的迭代循环
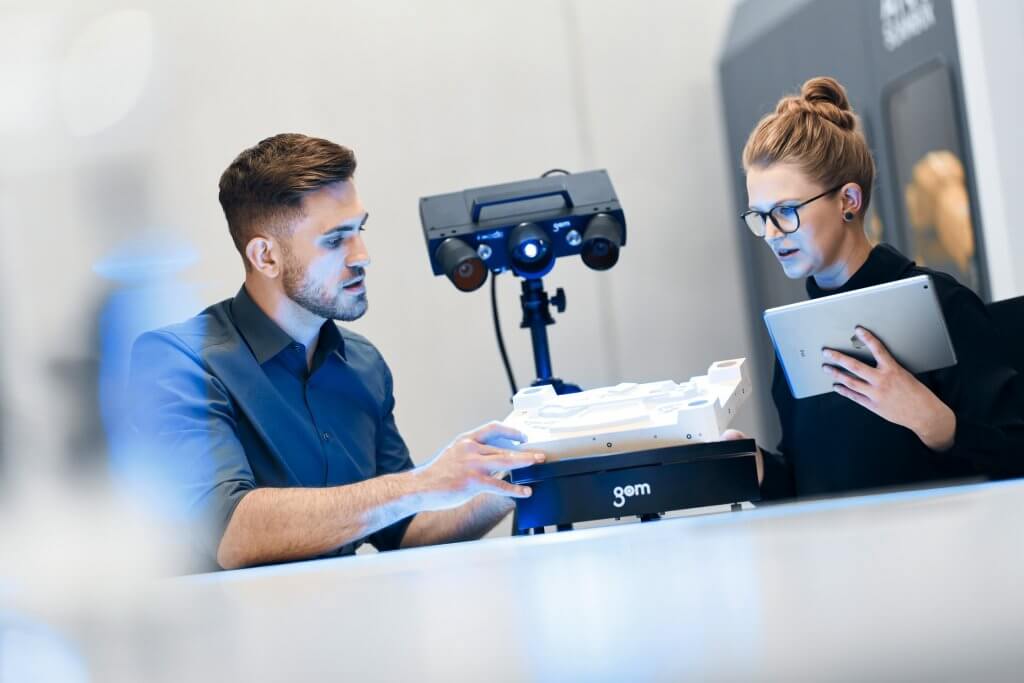
已发布工具的归档
如果在工具试用阶段手动修改工具,则工具会偏离设计数据。在 ATOS 系统的帮助下,可以通过表面重建来更新 CAD 数据。
挑战
工具试用阶段的常见情况:反复对工具进行各种手动更改,以生产具有正确几何形状的零件。这些变化导致工具偏离其设计数据。然而,工具的 CAD 模型应该准确地反映实际工具。
解决方案
如果用户使用 ATOS 系统在其整个表面上以 3D 形式扫描修改后的工具,他就能够可靠地记录对工具的任何手动更改并将其存档。这是因为 ATOS 测量数据提供了一个精确的数据库,用于通过逆向工程更新工具的 CAD 数据。
这种对已发布工具的归档可确保设计部门始终使用与实际工具相对应的 CAD 数据。这一设计的重要性体现在,例如,如果需要快速复制工具则无需再次经历试用阶段。
结论:以 3D 扫描铸坯有助于确定最佳铣削路径,避免耗时的“空气铣削”并防止加工工具断裂。
好处
- 可追溯的文档用于变更管理的工具调整;
- 永久更新——即使在手动更改工具后也可以保存CAD数据;
- 在工具损坏的情况下数据备份
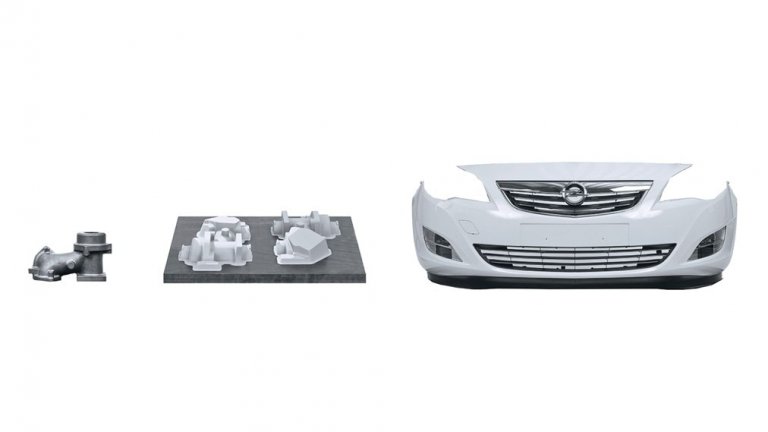
基于 3D 测量数据的仿形铣削
当需要更换损坏的工具或需要镜像工具变体时,可以根据 STL 数据直接铣削新工具,而无需事先进行表面重建。
为此,可以使用 ATOS 系统快速简单地对相应工具进行数字化。
收益
使用 ATOS 对工具进行 3D 扫描也很有用,无需将表面逆向工程为 CAD 模型。这是因为某些工具形状允许根据 ATOS 测量数据(STL 数据)直接铣削新工具。
例如,当需要更换损坏的工具时,这可能很有用。此外,也可以根据这些数据非常轻松地铣削零件右侧或左侧变体的镜像工具,无需再次进行试模。
好处
- 在没有表面重建的STL数据上直接铣削;
- 快防止工具损坏可以快速复制;
- 镜像工具易于生产