在全球化经济浪潮中,汽车制造业始终扮演着推动工业进步与技术创新的重要角色,伴随着工业的发展,汽车生产方式正经历着前所未有的变革,车身制造工艺技术中“一体压铸”技术也在不断更新和迭代。”
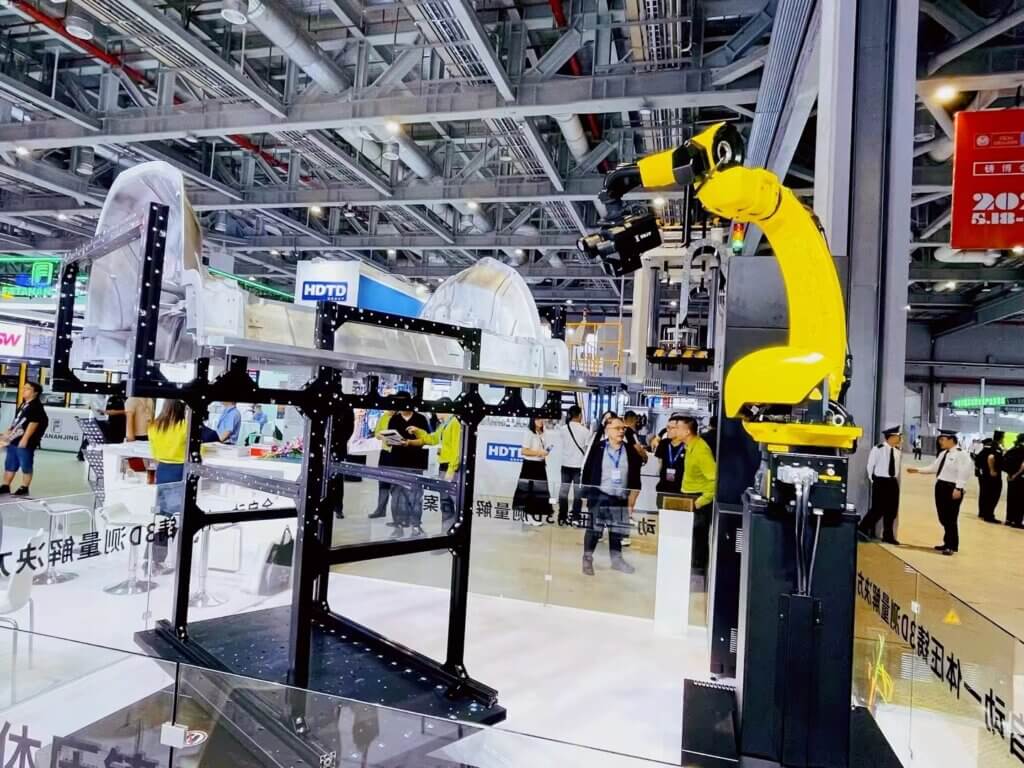
自2018年一体压铸技术概念首次被提出以来,这一技术便迅速成为汽车轻量化与效率提升的热门话题。
通过高压铸造工艺,直接将多个原本独立的部件整合为一个整体,不仅大幅减少了车身零部件的数量,还显著降低了尺寸匹配误差和焊接成本,为汽车制造商带来了前所未有的成本节约与生产效率提升。
然而,正如任何新技术在推广初期都会遇到的挑战一样,一体压铸技术也面临着其独特的难题。
面临的挑战
- 铸造的变形控制:由于一体压铸部件往往具有较大的投影面积和薄壁结构,在冷却过程中极易发生形变,这对最终产品的尺寸精度和装配性能构成了严峻考验。
- 复杂匹配需求:随着一体压铸部件在车身中占比的增加,其与整车各系统的匹配关系变得更为复杂,需要更高精度的尺寸控制和更细致的匹配分析。
- 3.质量检测难度:大型一体化部件的尺寸检测要求高,传统测量方法难以满足高效、精准的需求,增加了质量控制的难度。
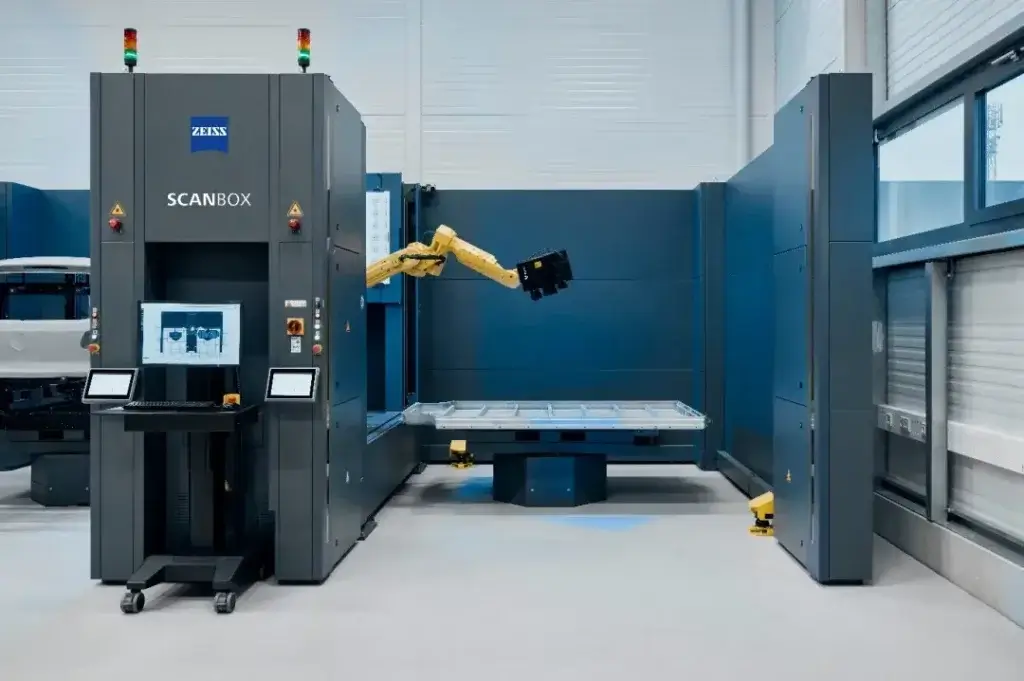
蔡司三维扫描技术的应对之策
面对这些挑战,蔡司的三维扫描产品以其卓越的性能和精确的测量能力提供了有效的解决方案。
ZEISS ScanBox自动化三维扫描系统,智能高效,精准测量!完美契合了大型一体化压铸部件所面对的尺寸要求复杂,节拍要求高,数据完整性要求高等问题。
- 智能示教技术,软件自动完成路径计算和扫描参数计算,减少人员工作,操作人员只需要专注于部件检测。
- 三重扫描技术,加速数据采集过程,更快速获取完整表面数据
- 大测量体积和高亮度光源,在短至0.2秒时间内即可完成千万级别的表面点获取,即使对于大型部件也只需要很少的拍摄,即可完成扫描。
- 自我监测技术,使得系统可以实时监控数据质量和测量环境,主动进行重标定和补测,以确保数据质量的稳定可靠。
- 全面的软件功能,可以实现如全域三维数据分析,壁厚分析,部件变形分析,加工余量分析,关键尺寸检测,GD&T尺寸检测等。
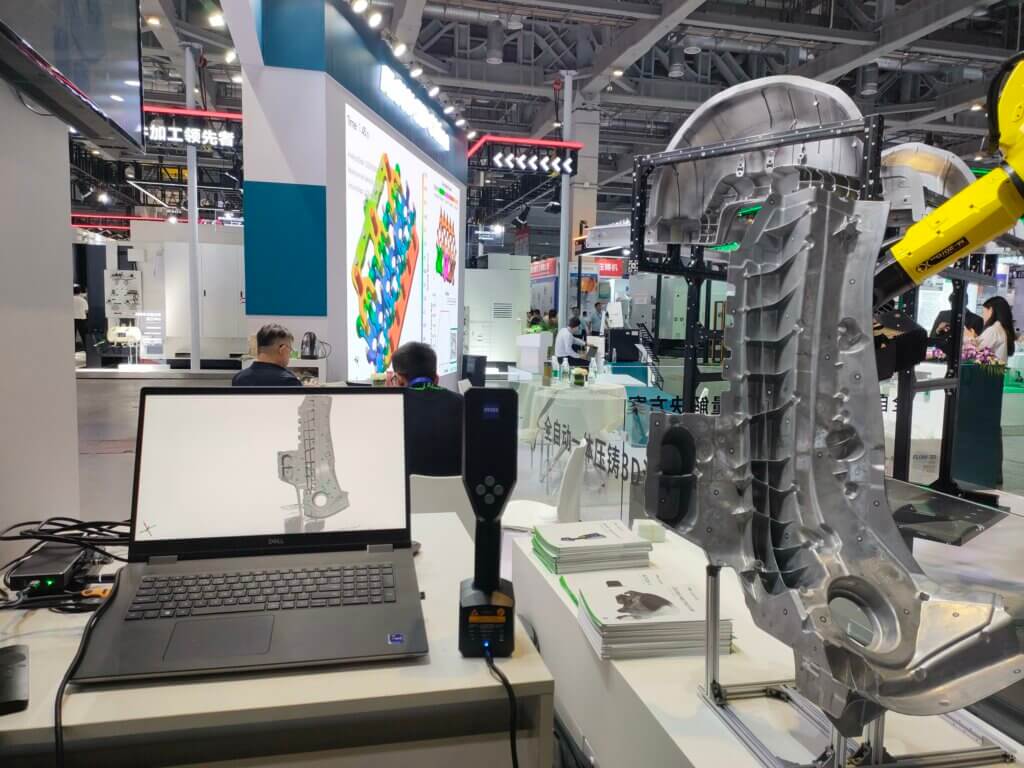
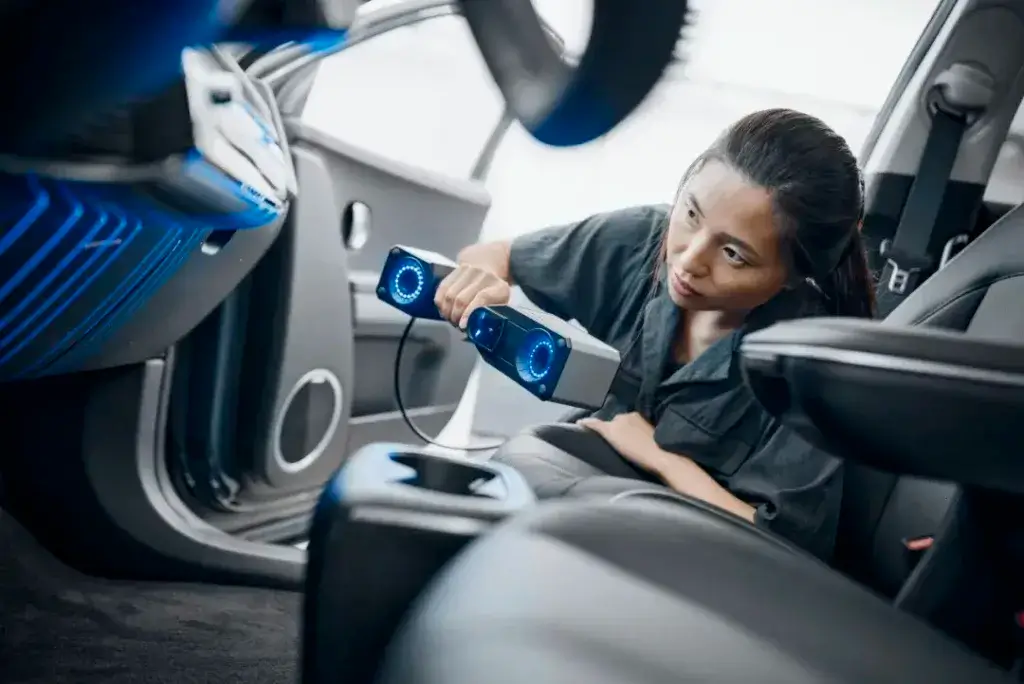