MolyWorks Materials Corporation (Molyworks) 与 3D Systems 合作,帮助满足其持续增长带来的不断增长的需求。 该公司购买了 3D Systems 的直接金属打印 (DMP) 解决方案,以增强其内部增材制造 (AM) 生产能力,同时扩大其客户范围。
凭借更大的打印量和独特的真空室功能,3D Systems 的 DMP Flex 350 解决方案提高了 MolyWorks 的敏捷性和效率。 这些动态改进加强了他们不断扩大的商业客户和政府机构关系,包括他们最近与美国空军的合作。
对于快速设计或产品迭代,3D Systems 的 DMP Flex 350 是无与伦比的。 通过在我们的设施中使用这个行业领先的解决方案,我们正在扩大我们对可以在我们的流程中进行 3D 打印的内容的愿景。
—Chris Eonta,MolyWorks 创始人兼执行官
MolyWorks 是一家总部位于加利福尼亚的金属循环经济开发商,已将 DMP Flex 350 和 3DXpert 集成到其制造工作流程中。 因此,MolyWorks 已经认识到其生产过程中效率的显着提高,以及通过向客户提供增材制造的最终用途部件来扩大能力范围的机会。
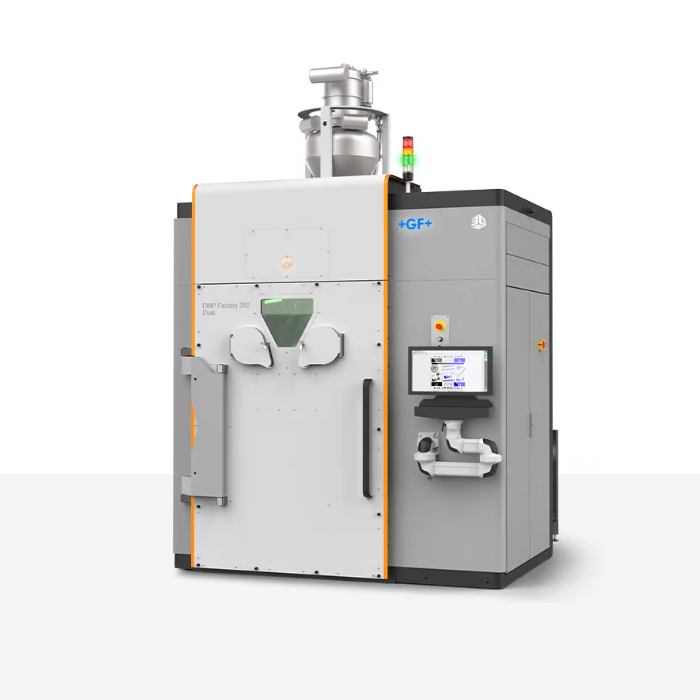
挑战:简化生产并扩大客户供应潜力
航空航天和国防 OEM 不断寻求通过创建尖端组件来优化他们的系统,这些组件可以通过设计优化来提高性能。 凭借其能够从现有废物流中回收金属的独特技术,MolyWorks 已经生产了 21 种用于陆地、空气、海洋和太空应用的合金。
为了满足客户在高度监管的航空航天市场中不断增长的需求,MolyWorks 寻求 3D Systems 的应用创新团队来扩展和完善其内部金属 AM 生产能力。
DMP 是一种 AM 技术,它使用由高功率激光熔化的金属粉末薄层,根据 3D CAD 数据构建高质量、复杂的金属零件。 DMP 提供了卓越的设计灵活性,并且不受传统制造的几何限制的阻碍。 借助 DMP,零件的制造成本对零件复杂性的依赖性大大降低。 这还可以通过缩短后处理链来帮助减轻供应链障碍。
解决方案:精炼钛生产
作为优质零件金属粉末生产商,为了适应其工作流程,MolyWorks 需要一种能够保持极低氧气水平的增材制造解决方案。 这有助于保持成品零件中的合金化学成分。
MolyWorks 选择 3D Systems 的 DMP Flex 350 是因为其独特的真空室结构,可以轻松保持非常低的氧分压 (>25 ppm)。 这对于具有严格的氧耐受性以控制机械性能的钛合金部件尤其重要。 除了保持极低氧气的制造环境外,真空室结构还减少了氩气消耗,并产生具有精细特征细节的出色表面光洁度。
“凭借其独特的真空室,我们能够将工艺过程中的氧气含量降至百万分之五。 DMP Flex 350 通过在成品部件中提供更好的化学控制和高水平的粉末再利用,与竞争机器相比具有不同的性能,”MolyWorks 增材制造总监 Devin Morrow 表示。
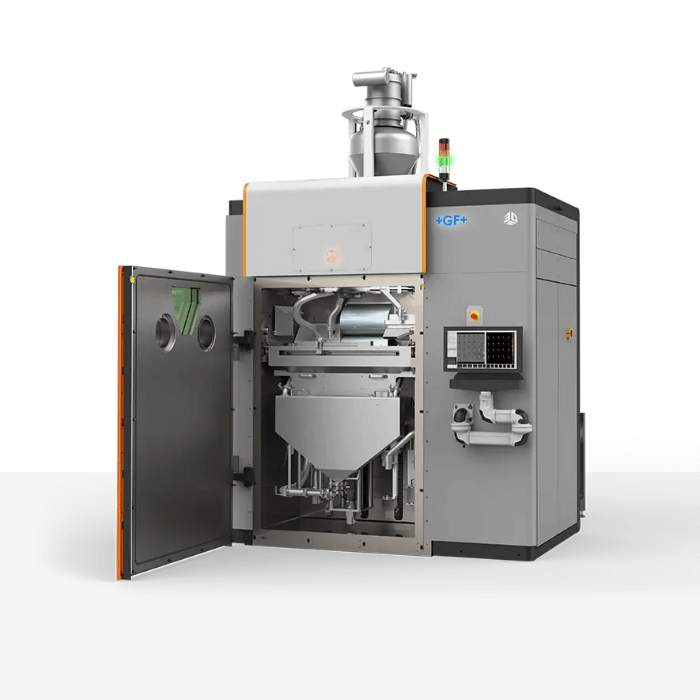
更高的应用灵活性和速度
在实施 3D Systems 解决方案之前,MolyWorks 受到较小的 3D 打印系统的限制。
借助 3D Systems DMP Flex 350,MolyWorks 可以促进快速设计和产品迭代以及整合组件的生产。 3D Systems 打印机上的可拆卸打印模块 (RPM) – 最大限度地减少了清洁和材料更换的停机时间 – 加速了 MolyWorks 的生产和认证过程,并缩短了开发周期。
“拥有 DMP 350 使我们能够以更快的速度进行更大规模的原型制作,”Morrow 说。 “如果我们要改用新合金,我们不希望需要数周时间才能重新上线。 有了这些内部机器,我们可以对同一零件进行 9 次不同的迭代,并快速将它们轮换出来。”
简化设计到生产
DMP 非常适合生产具有复杂或不规则形状、内部通道、复杂表面纹理和内部晶格的紧凑型组件。
3DXpert 在实体模型上运行,直接来自常规工程设计过程。 无需处理中间的、有问题的 STL 文件。 直接从 CAD 文件中 3D 打印零件可以显着缩短从概念到设计再到制造零件的时间,而不会失去特征保真度。 带有 Oqton 的 3DXpert 软件的 3D Systems DMP Flex 350 支持 AM 工作流程的每一步——从设计到构建准备和建模。
使用 3DXpert,MolyWorks 工程师可以在同一个界面中支持结构生成、晶格设计和衍生式设计。 这个单一的软件解决方案提供了在同一部分中混合和匹配其中一些策略并将其保存在一个地方的能力,从而消除了对多个软件包的需求。
“能够从 3DXpert 中的设计和优化无缝过渡到使用 DMP Flex 350 的生产,这确实帮助我们简化了流程,”Morrow 说。
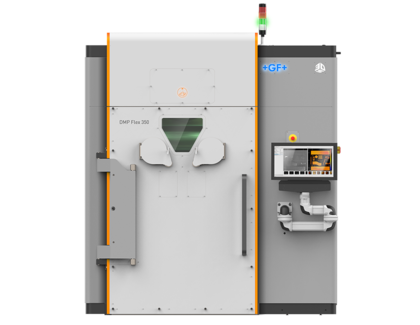
更大规模的制造
DMP Flex 350 拥有中框 LPBF(激光电源床融合)系统中可用的最大构建体积之一(275 毫米 x 275 毫米 x 420 毫米)。 这个更大的构建体积,超过了大多数竞争系统的大小,允许完全的灵活性。 除了打印大型组件外,该空间还可用于打印多个较小的组件或将组件合并为更大、更高效的单元化组件。
这种扩大的内部生产能力帮助 MolyWorks 扩大了业务,包括与五个美国政府机构和其主要领域的基石商业客户合作:医疗保健、汽车、航空航天、国防、石油和天然气以及能源。
“借助 3D Systems 单元,我们从制作一个或两个组件转变为在一个构建中使用 10 多个组件进行完整构建,”Eonta 说。 “我们用这台打印机生产的起落架部件的质量给我们留下了深刻的印象,这些部件将进行适航性测试,我们期待着我们将解决的其他应用。”