本应用简报由Erlangen-Nuremberg大学金属科学与技术系主任,材料科学系Johannes Hartmann和VeraJüchter提供
铝泡沫显示出优异的性能,如良好的阻尼,高能量吸收和质量比弯曲刚度[1]。刚度使其在承重和同时使用轻质结构时尤其具有吸引力。为了提高这种重量比刚度和更好的载荷传递,需要一个紧凑的外壳[2],如在铝泡沫三明治(AFS)中实现的那样。
Erlangen-Nuremberg大学金属科学与技术系主任研制了改进的压铸工艺“整体泡沫成型(IFM)”,以生产具有完整实心表皮,发泡芯和渐变的铝泡沫过渡区之间(见图1)。该工艺是由聚合物的发泡注塑成型开发的,因此适用于具有紧凑层的复杂泡沫部件的成本有效的一步式大规模生产。本说明中描述的CFD软件Flow-3D模拟技术已被用于对此过程进行建模,作为选择过程参数的辅助手段。
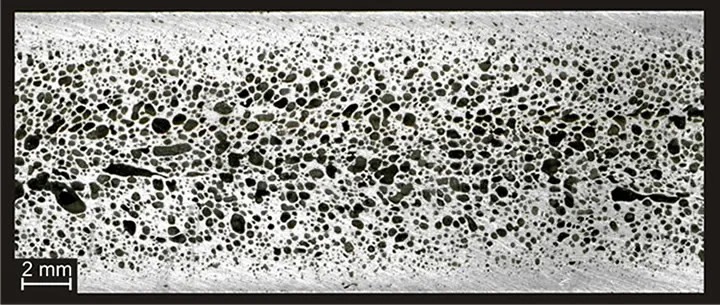
铝泡沫整体式成型技术
因此,一定量的发泡剂(氢化镁,MgH2)被放置在流道系统中,并且喷射室充满铝熔体(示意性工艺循环如图2所示;该过程在[3]中详细描述) 。随着活塞前进,粉末以紊流方式夹带到模具中。在技术变型“高压一体式泡沫成型(HP-IFM)”的情况下,该零件在标准压铸工艺中已知的高环境压力下完全填充,从而确保出色的表面质量。从模具的回火表面开始,熔体开始凝固成完整的固体表皮。几毫秒后 – 即所谓的延迟时间 – 模具在抽芯系统上打开,体积局部增加(并减小压力),由于热分解和氢释放,在内部半静态区域开始孔的生长的氢化镁颗粒。每个发泡剂颗粒代表孔生长开始的孔核,直到它被同时膨胀的相邻孔的反压停止为止。由此形成的单元壁通过主要凝固的铝合金颗粒稳定化,所谓的内源稳定[4]。每个发泡剂颗粒代表孔生长开始的孔核,直到它被同时膨胀的相邻孔的反压停止为止。由此形成的单元壁通过主要凝固的铝合金颗粒稳定化,所谓的内源稳定[4]。每个发泡剂颗粒代表孔生长开始的孔核,直到它被同时膨胀的相邻孔的反压停止为止。由此形成的单元壁通过主要凝固的铝合金颗粒稳定化,所谓的内源稳定[4]。
在铸造部件的整个体积中均匀泡沫形态的先决条件是在分解开始时颗粒的良好分布。此外,发泡剂夹带期间熔体的温度一方面决定氢化镁的分解动力学(参见图3),另一方面决定发泡过程中固相的量。由于毛细作用力引起的熔体排液导致毛孔粗化,固化的α-晶粒不足导致形成相邻孔之间的非稳定支柱。然而,大量的固相增加了基体的刚性,并通过阻碍发育孔的球化导致结构破坏[2]。
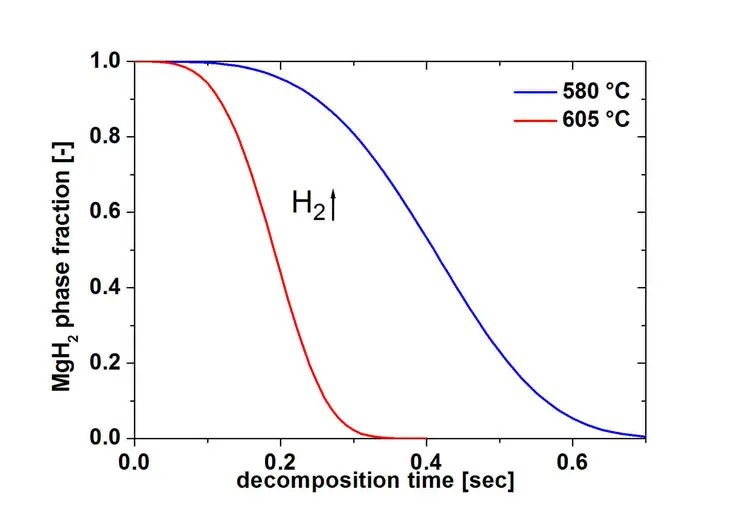
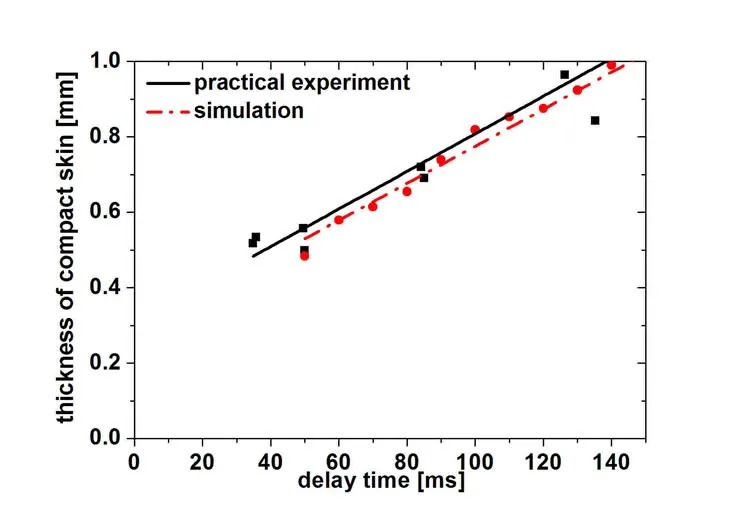
将仿真参数调整为实用的整体泡沫成型实验
为了能够使用 Flow-3D 的 CFD模拟来预测颗粒行为或温度场的可靠性,必须通过调整这些参数以匹配实际实验来确定不同的模拟参数。为此,整体式泡沫部件的生产延迟时间大约介于5秒之内。30和130ms导致不同的致密的表皮厚度,其中由于固相分数超过一定百分比而不可能形成泡沫在模膨胀和孔生长开始的时刻。这导致了一个特征性的所谓的凝固曲线,其轴截距和斜率取决于模具温度和其他选择的工艺参数(见图4)。通过改变传热系数(完全液态熔体的值以及完全固化的熔体)来模拟合金AlSi9Cu3(Fe)的铸造周期,可以拟合实验凝固曲线。为了实现这一目标,有必要将模拟延伸到射流室中的熔体计量,以描绘活塞运动开始之前的实际温度分布。通过放置热电偶在射击室局部测量温度,并且可以成功描绘与模拟内的真实数据非常吻合的温度。
在第二步中,使用Flow-3D定义熔体流动行为(例如表面张力或凝固阻力系数)的其他参数 通过将不同设置的模拟与在填充模具之前活塞停止的实验研究(参见图5)进行比较来调整。一旦模拟内的熔体流动与实际测试一致,就设定参数。
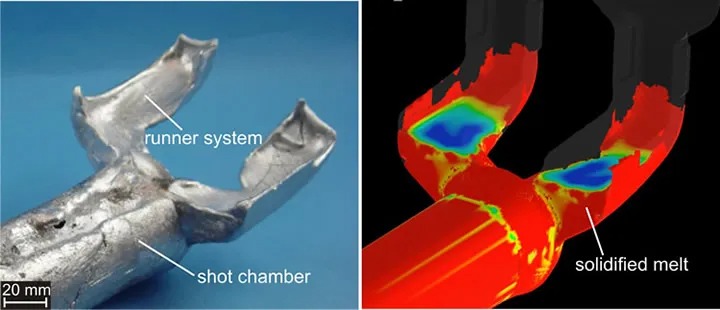
在确定冷却以及熔体的流动特性之后,模拟颗粒的夹带。为了调整正确的颗粒/流体相互作用的模拟, 通过比较X射线样品来拟合颗粒阻力的颗粒定义参数 系数,其中在X射线表征中具有比氢化镁高的对比度的替代颗粒是铝夹带,例如铜或铁颗粒(见图6)。模拟结果与实验非常吻合,因此可以推断粒子分布的可靠预测作为过程参数的函数。
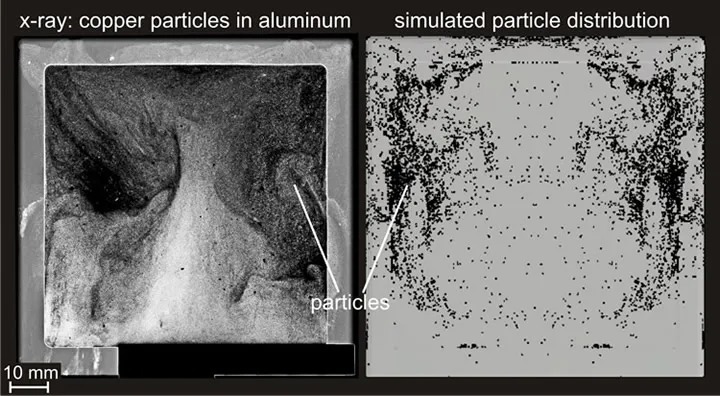
结论
总之,可以证明 FLOW-3D 模流分析软件可以成为找寻在实际生产之前制造新整体泡沫部件的潜在弱点的重要工具。这样就可以保证无冷流或死区的成功填充和发泡剂分布。此外,由于预期的温度场的正确描述,可以推断形成致密的表皮和氢化镁的分解性质(以及因此孔形成条件)。这提供了定义工艺参数以满足客户对整体泡沫结构的要求的潜力。
1 标准是固体相部分,其中剪切强度和因此孔隙演变的阻力急剧增加。