在今日的市场环境中,大部分企业都同时面临旧有完善制度与新的快速增长经济需求的压力。市场的全球化强迫企业寻找可以持续维持竞争优势的方法,而互联网技术的快速发展以及信息的自由交换,将是让公司能够保持竞争优势的主要因素。
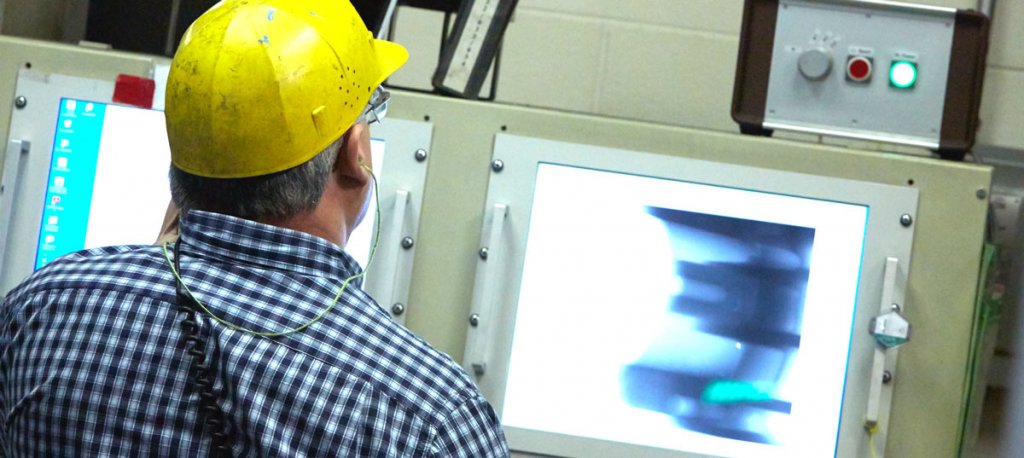
对于企业而言,在行业中保持领先地位的方法之一,是缩短将创新技术带入市场所需的时间。为了压缩压铸工艺开发时间,使用FLOW-3D进行建模以及仿真模拟已成为Shiloh Industries工程部门不可或缺的一部分。
在Shiloh Industries,每一个新项目都必须从浇口与流道系统的概念设计、料管速度-行程估算、料管直径、最小排气面积以及制程所需压力开始检讨。利用数值模拟分析开发出最佳的流动模式以及最小的卷气设计。完成流道设计后,再进行热传分析,以协助决定冷却水路的配置方案。
FLOW-3D最吸引人的特色,在于其能够为开发过程的每个阶段运行单独的分析。它能够让使用者在短时间内协助决定最佳的料管行程设定、浇口设计,以及水路配置。然后利用单次的流动-热传耦合计算,验证所有的设计都能够完美的运作。另外,利用FLOW-3D的 GMO模型还能够真实模拟柱塞在料管压射阶段的运动方式,对于项目开发而言,零件设计已经从单独的产品转换成真实的量产。
案例说明
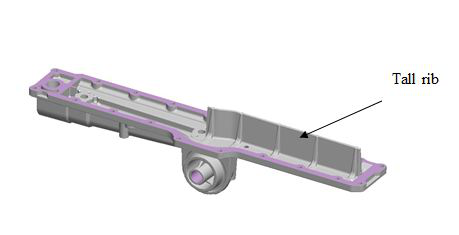
图一的铸件对于铸造制程而言,是个较困难的产品。主要的关键在于铸件上凸出的肋件特征,对于金属融汤流动及凝固时会造成困难,导致铸件质量不易兼顾。肋件特征在凝固及冷却阶段会造成热应力集中,让铸件发生不预期的变形。
在设计初始阶段,开发人员提出了二十一种不同的流道方案设计,并且利用FLOW-3D验证所有的流动模式。图二为这二十一种方案中其中的三种流道设计。
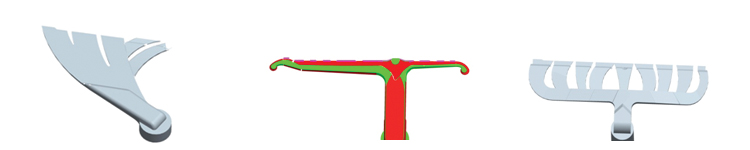
在流道方案设计验证中,流动模式是决定流道方案成败的关键因素。在初始流道设计阶段结束后,决定采用图二中的第二种及第三种设计进行接续分析。
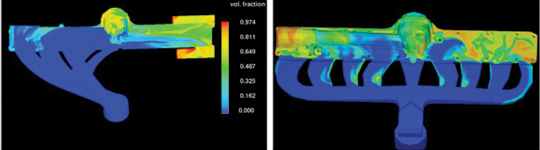
第二阶段的验证分析则是凝固分析。此时铸件的温度分布将是决定方案优劣的关键因素。图四中显示采用图三右图设计方案时,凝固阶段结束时之温度分布结果。
