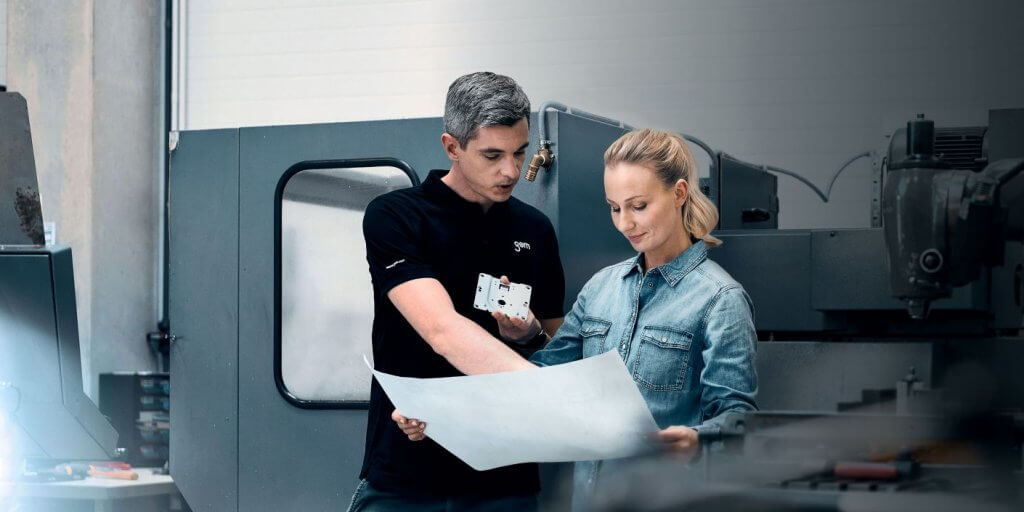
制造
铣削铸坯,制成模具。测量系统首先将铸坯数字化,并将其与CAD模型对准。然后,超出的部分会直接进入铣床。这种做法可以使数控机床的运行时间缩短高达50%,同时最大限度地减少刀具磨损。
试模
模具生产出来后,必须进行试模,从而检测试模件是否与设计相匹配。为完成这项工作,测量工程师需在冲压车间内扫描此部件。利用全域测量资料,GOM检测软件能够识别出该数字孪生模型与CAD资料之间的偏差。问题区域一目了然,从而对模具进行修正。
归档
为了使生产出的部件具有准确的几何结构,往往会在试模阶段叠代过程中重新制作模具。然而,经过手动修改之后,该模具就不再与CAD模型适配。因此,CAD模型也需要进行升级才能归档。为此,需要对修改后的模具进行全域扫描。之后便可以通过逆向工程轻松更新CAD资料。
仿形铣削
即便不用逆向工程,在CAD系统中利用三维测量资料和特定形状的模具,也可以铣削新模具。这在替换损坏的模具时很有帮助。此外,这些资料还可以用作镜像模具简单铣削的基础。
修理
模具总会有磨损到不得不修理的一天。将数字孪生模型与CAD资料进行对比,可以看到模具上的关键磨损区域。由此,可以精准焊接材料到某个特定的点进行修理。焊接后出现的任何多余的材料都可以通过再次扫描模具被快速识别,便于重新铣削。